Fig. 83.1
Penetration depth study for various polymer materials, imaged at 840 and 1,550 nm: polyamide (PA), polyamide filled with glass fibers (PA + GF), polyether ether ketone (PEEK), polyoxymethylene (POM), polyethylene (PE), polypropylene (PP) (Reprinted with kind permission from Springer Science + Business Media: Fig. 6 from: D. Stifter, “Beyond biomedicine: a review of alternative applications and developments for optical coherence tomography,” Appl. Phys. B, vol. 88, p. 337, © Springer 2007)
All polymer samples of this study exhibited a similar visual appearance (e.g., level of turbidity), and complementary absorbance measurements in reflection geometry in the visible and near-infrared wavelength region between 500 and 2,500 nm also showed no significant differences between the specimens. Nevertheless, they all performed differently when imaged by OCT. In order to determine the overall penetration depth for the two selected wavelength regions, the polymer wedges were imaged by OCTs which were adjusted to the same sensitivity level. The arrows in Fig. 83.1 represent the level of depth where the backside of the sample is still visible, i.e., simulating a void structure in the polymer bulk. The additional arrows in the 1,550 nm images on the left side are marking for comparison the penetration depth measured at 840 nm. Since light absorption by water is usually of no concern for polymer imaging – a fact which holds true for most technical materials – longer wavelengths are in general more favorable for larger imaging depths due to decreased attenuation by scattering [6]. In the example of Fig. 83.1, the scattering behavior is influenced by the different internal morphologies of the polymer samples with crystallites and granular structures of varying length scales. Since the solidification and crystallization behavior of polymer melts is largely dependent on the processing conditions (e.g., temperature, pressure, flow velocity, and shear field gradients in polymer extrusion and injection molding [7]), the situation further complicates, as does the addition of various kinds of fillers (e.g., short glass fibers, talcum, silica, carbon particles, etc.) and pigments to the polymer material, exemplified in Fig. 83.1 for the polyamide (PA) sample filled by 30 wt.% with short glass fibers (GF).
An analogous situation as for the above-presented bulk polymer samples holds true for other material systems. Consequently, for a new envisaged NDT task, a thorough feasibility study for the material or structure of interest will mostly be necessary, although all types of (semi-)transparent media are in principle eligible for OCT imaging. To date, OCT studies have been carried out and reported for a variety of (partly natural) materials, among which can be found:
Polymers, in the form of bulk material as well as thin films, including paints, organic coatings, layers of adhesives, and bonding agents
Paper, papyrus, wood, leaves, fruits, and seeds
Semiconductors
Metal oxides and corrosion products
Glass, ceramics, and ceramic glazes
(Semi-)precious stones and pearls
…
The potential applications for OCT multiply when considering composite structures made from the above-listed materials, like glass fiber-reinforced polymer materials with enhanced mechanical properties, micro (opto-)electro-mechanical systems (MEMS, MOEMS) or encapsulated multilayer organic solar cells. A detailed description of already identified applications and results from feasibility studies performed on the above-listed materials and combinations thereof – as reported in literature – is now given in the following.
83.3 Applications of OCT for NDT
In contrast to biomedical OCT imaging, with the diagnostics of retinal diseases being the main driving force for commercial scanners, it has to be stated that no analogous killer application could yet be identified for OCT in NDT. However, several material imaging and evaluation studies have been carried out, which already led in some cases even to routine tasks in NDT/NDE with corresponding commercialized OCT scanners and measurement devices.
In this context it is useful to reconsider at first the different types of application areas which take benefit from NDT: the preservation of the original status of a sample is of utmost importance not only in industry, e.g., for the investigation and quality control of final products, but also of products being in an intermediate manufacturing status prior further costly or time-consuming processing steps, most preferably carried out in situ and without introducing additional delay. Likewise, precious or unique objects should also not be altered by the applied investigation method, a task experienced, e.g., in the evaluation of gems and pieces of jewelry, but mostly now emerging in the field of art and cultural heritage conservation [8]. Finally, also for research and development, the nondestructive character of an investigation method is needed, especially if the same sample has to be characterized by additional methods in order to learn about complementary properties or if the same sample has to be repeatedly measured in case of time-dependent investigations, like ageing and degradation studies. On shorter time scales, investigations which also can be of destructive nature, as, e.g., mechanical tests, take benefit from continuous nondestructive monitoring in order to study the performance of a single specimen. Summarizing, in the following general situations, NDT methods are indispensable, namely, for:
(Industrial) quality control of final products (also online)
Guidance of the production process itself (preferably in situ or online after crucial processing/manufacturing steps), including:
Full, 100 % quality control
Investigation of small representative areas from each sample
Batch inspection by taking samples (off line, on site)
Evaluation of precious or unique samples like:
Precious stones, gems, and pearls (for classification purposes)
Art objects for archaeometry, conservation, and detection of forgery
Documents, banknotes, etc., for applications concerning security
Research and development
Nondestructive material characterization before or during complementary investigations (e.g., fracture tests), leading also to
Repeated measurements on the same sample over time, and including
Studies of physical phenomena which are not directly accessible or easily influenced (e.g., flow behavior of liquids)
For the above-listed points, several instructive examples of OCT being successfully applied have been reported and are laid out in the next sections. They are listed according to the category of information obtained from the individual measurements, starting with the evaluation of the pure surface structure, proceeding to thickness measurements of layered systems, to imaging of internal 3D structures and finally leading to the determination of functional information.
83.3.1 Surface Metrology
The principle of white light or low-coherence interferometry (WLI, LCI) was already used in the 1980s for remote sensing of distances in an unambiguous way, e.g., in a point-wise sensing style like standard OCT with fiber optics [9] or by using area sensors for parallel detection [10]. The latter technique, being called coherence probe (CP) imaging, uses a Linnik interferometer in a basically similar setup as full-field (FF) OCT [11] and was immediately introduced for the measurement of surface topographies, with fully automated metrology systems for the inspection of line widths and defects of resist structures on Si wafers [12]. Further developments focusing on the profilometry capabilities of this technique soon followed, including a coherence scanning microscope in Michelson configuration [13] or a Mirau correlation microscope [14] with increased stability against vibrations and providing amplitude and phase information for accurate surface measurements as demonstrated on photoresist trenches for integrated circuits. Interestingly, the sectioning capabilities for such CP or correlation microscopes when using medium-to-high numerical aperture (NA) objectives do not solely rely on the temporal coherence properties of the light source (which is mostly also spatially incoherent) but also on the fact that interference can only occur for regions on the sample where the curvature of the wave front matches (correlates with) the one of the reference field [15]. Only, when using such full-field detectors for thicker object structures, the noninterference background image is – compared to conventional OCT – not sufficiently suppressed, which can lead to detector saturation and decreased sensitivity. However, these techniques were most successfully further developed for the investigation of surfaces, leading to, e.g., scanning white light interferometers (SWLI) which are nowadays routinely used for topography measurements, providing even subnanometer precision on smooth homogenous surfaces by an evaluation of the phase or phase slope information [16]. Equally, dedicated profilometers for rough surfaces have early been reported [17] and applied, e.g., as so-called coherence radar on high aspect ratio features (up to 2 cm deep bore holes with 5 mm in diameter) of machined industrial parts [18].
Simultaneously to the full-field approaches described above, the point-wise detection scheme of conventional OCT, generally using fiber optics together with spatially coherent sources and exhibiting shot-noise-limited performance, emerged [1]. Here, the detection of weak backscattering features, in contrast to the evaluation of the strongly reflecting air/surface interface, was of prime interest, inspired by the optical low-coherence and coherence-domain reflectometry (OLCR, OCDR) techniques which were originally introduced for the characterization of optical waveguide components [19, 20] and already used for depth measurements of trench structures in memory chips [21]. Since both approaches, i.e., full-field CPM vs. conventional point-wise scanning OCT, have their same origin in LCI, OCT is repeatedly subject of surface evaluation studies including surface shape [22] and roughness measurements [23]. In this context also efforts in, e.g., providing validated procedures for reliable surface characterization with OCT, which are conform and linked to recognized standards, are essential [24]. However, one has to mention that OCT might not always be the first choice for such surface metrology tasks: especially for easy accessible surfaces with moderately inclined slopes and features, OCT has to compete with other dedicated commercialized surface metrology devices based on techniques like confocal microscopy [25], the above-introduced SWLI, wavelength scanning interferometry (a swept-source (SS) variant of WLI in the Fourier domain (FD)) [26], digital holography [27], or chromatic confocal microscopy (CCM) [28], a principle which relies on chromatic length aberration of specialized lenses to measure distances and results in simple, robust, and cost-effective sensors. These techniques were even further enhanced: e.g., CCM can be combined with the principle of spectral interferometry (SI) – similar to spectral-domain (SD) OCT – to form a hybrid chromatic confocal spectral interferometry (CCSI) sensor for surface metrology of uncooperative surfaces, taking profit from the interferometric gain (like OCT) and from the evaluation of the phase [28]. Nevertheless, OCT systems and dedicated OCT-like sensors were commercialized and are increasingly offered for surface metrology (although such commercial devices are sometimes even not referring to OCT but are just simply called interferometric or topography sensors), with advantageous performance especially for the evaluation of high aspect ratio structures, specularly or very weak reflecting slopes, and – by using fiber-optic sensor tips or thin needles – for areas which are hard to reach, like the interior of bore holes, tubes, and cylinders.
An example for the topography evaluation of high aspect ratio features is given in Fig. 83.2, with laser-drilled holes, exhibiting an average depth of 1 mm and an average width at mid-depth of 100 μm, in a carbon fiber-reinforced carbon (CFC) composite structure. Such structures are used in the so-called divertor of nuclear fusion reactors and need efficient cooling, realized by interlocking these structures to a layer of copper. Due to the rough nature of the surface in the inside of the holes (partly caused by exposed fiber ends during machining), the strong inclination, and increased light absorption by carbon, conventional surface metrology tools (like SWLI and confocal microscopy) failed. In contrast, the high sensitivity of OCT ensures that the topography can successfully be traced down to the bottom of the holes. Comparative dimensional measurements on polished sections as well as by X-CT have proven the accuracy of OCT and were leading to a dedicated OCT-based inspection system with automated image evaluation [29].
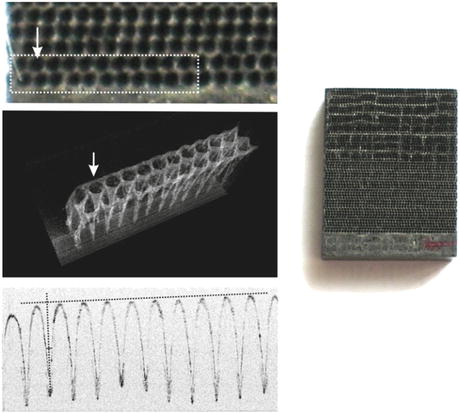
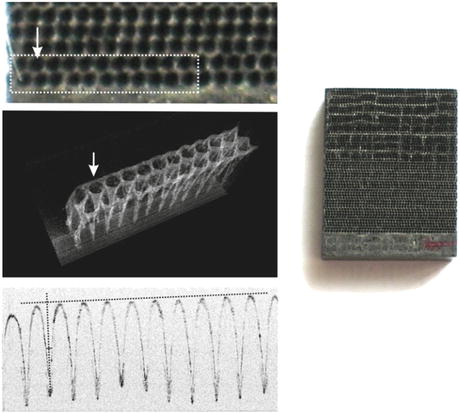
Fig. 83.2
Laser-drilled holes with high aspect ratio in a CFC structure evaluated by OCT. Top and right: photograph of sample and enlarged surface area indicating the reconstructed volume measured by OCT (middle). Bottom: cross-section through one row of holes, with an average depth of 1 mm and an average width of 100 μm at mid-depth. (OCT software by M. Wurm, UAR GmbH, Austria), (Sample courtesy of Plansee SE, Austria)
Further reported examples for surface profilometry with OCT include the shape determination for grinding optical lenses [30, 31] or surface roughness measurements on paper [32] and pharmaceutical tablets [33]. OCT was also used to evaluate the response of surface cracks on an artistic painting as well as deformations of the canvas during humidity changes [34]. In addition to the examination of silicon V-grooves [35], MEMS structures [36] and the determination of shape and deformation of semiconductor wafers [37], real-time reflectivity and topography measurements of integrated circuit (IC) structures with FF-OCT [38] and topography measurements of MEMS and ICs from phase maps with SS-FF-OCT [39] were reported.
Modified OCT techniques were used, e.g., to determine the topography of metallic surfaces, like ball grid arrays or electrodes with a so-called parallel OCT system [40, 41] where each pixel of the 2D detector array has an own demodulation circuit, or to quantitatively reconstruct surface profiles (like those of microlens arrays) by differential phase-contrast OCT [42].
Finally, it shall be mentioned that the high sensitivity, robustness, and rather long-working distance of such OCT-based sensors and systems render them very suitable for online monitoring during machining/processing as well as for the quality control of moving parts. In the context to the above-presented example of Fig. 83.2, in situ monitoring of laser drilling, structuring, and machining of materials like steel, ceramics, glass, or polymers [43–46] even with automatic real-time guidance [47] was reported or – in the field of art diagnostics – the in situ monitoring of laser ablation for removing aged varnish layers from paintings [48]. Further applications also include OCT/LCI measurements simultaneously performed with laser-induced breakdown spectroscopy (LIBS) for complementary elemental analysis [49, 50]. With respect to surfaces, which are not easily accessible, metering the level of liquids (e.g., of molten glass in glass melting ovens [51]) or gauging in-line hot float glass [52] shall be mentioned, as well as a study for the in situ determination of the roughness of chemical mechanical polishing pads for semiconductor wafers which are covered by a wet and slurry containing layer [53]. The last example leads to the application of OCT to provide a profile of a buried/coated surface, as demonstrated for the dynamic monitoring of the drying process of varnish on paint in order to study the formation of surface roughness [54], for analyzing (varnish-covered) imprints of tools which were used for gold punch decorations as found, e.g., on Renaissance panel paintings [55], as well as for buried topographies of printed electronics (e.g., radio-frequency antenna) in a comparative study with topography measurements by WLI and contact profilometry [56].
83.3.2 Thickness Evaluation of Layers and Thin Films
The acquisition of profiles from buried surfaces immediately leads to the determination of layer and film thicknesses, a task where OCT has equally to compete with a variety of other optical techniques like with the above-introduced chromatic confocal principle or with (spectroscopic) reflectometry or ellipsometry [57], which are routinely used, e.g., in the semiconductor industry for layers ranging from several hundreds of micron down to (sub-)monolayers. As to the original LCI techniques, one of the first motivation was to use a Michelson interferometer as a remote gauge for distance measurements between two reflecting surfaces [58]. Thickness measurements of dielectric layers on metal surface by coherence scanning microscopy followed [13], which naturally lead to the extension of WLI for the characterization of layered structures [59], as nowadays routinely used and exemplified, e.g., with SWLI for the evaluation of transparent thin films in MEMS and MOEMS devices [60]. In this context, it has to be also noted that an abundance of variations and modification of the abovementioned LCI and OCT-like methods for surface profilometry and thickness metrology exists. One example is spectrally resolved line-field interferometry, for which a 2D detector as in CPM or FF-OCT is used, but the light is spectrally dispersed in one direction on the detector chip (like in spectral-domain OCT (SD-OCT) using 1D cameras) and a line from the sample is imaged along the other axis. In such a way 1D thickness profiles of transparent thin films on patterned surfaces can be acquired in one shot [61], as it was demonstrated before for pure surface metrology [62, 63].
From these examples, it follows that conventional OCT can also be used as a distance gauge for plane-parallel surfaces/interfaces delimiting transparent and non-scattering materials. In such cases one has to cope with artifacts arising from, e.g., multiple interference [64]; however, the determination of the thickness of single semiconductor wafers or multilayer semiconductor structures, as demonstrated in [65] for wide band gap materials as GaAsP/GaP heterostructures, is quite straightforward. Also wafers of silicon (with a band gap of ∼1.1 eV) are equally transparent [66] and suitable for thickness measurements when using the 1,300 nm and 1,500 nm wavelength range. Such evaluations are especially important in the context of wafer back grinding and etching to ensure the required uniformity in thickness together with a characterization in terms of flatness and bow/warp, parameters which have to be optimized for a successful 3D integration of (opto-)electronic devices by wafer stacking.
In order to obtain the true geometrical thickness of layers, the refractive index has to be known, as it is usually the case for standard semiconductor materials. If an unknown overlayer is situated on top of a nominally flat substrate (e.g., on a polished wafer surface) and exhibits thickness variations or lateral structuring, the determination of the refractive index is also easily accomplished by evaluating the deviation of the imaged substrate profile from a straight line [67, 68]. In general, however, focus tracking can be used to determine simultaneously with the thickness also the (group) refractive index [69, 70] or phase and group indices, and thickness [71]. The hardening process of UV-cured epoxy was monitored in such a way by detecting variations of the refractive index [72]. Finally, refractive index profiles of graded refractive index rod lens could be determined by iterative fitting of the optical path length calculated by ray tracing [73].
In addition to the examples involving thickness measurements given above, the full potential of OCT is exploited for samples where the type and strength of the reflectivity of the individual surface and interfaces strongly differ, e.g., for a smooth layer on a rough surface or a weakly reflecting coating on top of a mirror-like metallic surface, as well as for complex multilayer structures, and – most important – for layers with embedded scattering features which can obscure the underlying interfaces. In these cases, the conventional measurement approach using SWLI, CCM, confocal microscopy, and related techniques mostly fails and calls for the high sensitivity and depth discrimination capability of OCT. The evaluation of complex and not fully transparent multilayer polymer foils is consequently one example, where OCT can efficiently contribute, as shown in the example of Fig. 83.3 by using an ultrahigh resolution (UHR) OCT for imaging in the 800 nm wavelength range [67]. The multilayer structure itself consists of two welded foils with a total of 12 individual, partly scattering layers. These individual layers define the mechanical properties and partly represent different gas diffusion barriers, as required for modified atmosphere packaging in the food industry.


Fig. 83.3
Cross-section of a welded structure from two polymer multilayer foils for thickness evaluation, with a thermally damaged region (indicated by arrow) (Reprinted from: K. Wiesauer, M. Pircher, E. Götzinger, S. Bauer, R. Engelke, G. Ahrens, G. Grützner, C. Hitzenberger, and D. Stifter, “En-face scanning optical coherence tomography with ultra-high resolution for material investigation,” Opt. Express, vol. 13, p. 1015, 2005, with permission from the Optical Society of America © 2005)
With the advent of high speed acquisition by FD-OCT, on-line thickness measurements of such multilayer foils during the production, e.g., by blow film extrusion, can successfully be performed to control the correct dimensions of each layer, by simply using a static point sensor and monitoring a 1D profile of the foil, which is normally moving at a velocity of several tens of meters per minute. Even solutions to cope with the adverse conditions during production, like fluttering of the foils, have been developed: ambiguous mirror terms when the sample crosses the zero optical path delay can be suppressed by, e.g., tailoring the sensitivity profile in SD-OCT with a hardware-based approach and without the need of additional data post-processing [74].
As to the characterization of other layered 2D material systems, the thickness measurement of coatings on high-quality glossy photo-paper has been shown as well as that – in some cases – imaging through the entire thickness range of some kinds of paper sheets is possible [75]. However, typically the imaging depth is limited to tens of micrometers for ordinary paper, and a clearing agent (like benzyl alcohol) is needed to detect the backside due to the high scattering properties of the fiber network and the embedded fillers [76].
A similar role of the glossy top coating on paper (beside influencing the printability) plays the varnish layer on artistic paintings by enhancing the visual appearance and color saturation due to reduced diffuse scattering from the rough paint surface and increased specular reflections (away from the observer’s eye) from the smoother varnish surface. A dedicated task in art conservation is the removal of aged varnish, as already pointed out in the above section. Thus, precise knowledge of the thickness as well as information on multiple layers of varnish being potentially present is crucial for a gentle restoration procedure. Similarly to the evaluation of thicknesses and structure of varnish layers [77–80], also paint layers themselves are of interest. However, they usually show quite high absorption and decreased penetration caused by scattering, especially in the visible wavelength range. Imaging at longer wavelengths seems preferable, as proven, e.g., in a comparative study using a 820 nm and 1,550 nm OCT system for a variety of different commercially available artist oil paints [81]. In this context, it shall be noted that also the thickness determination of industrial paint layers and multilayer paint systems is a challenging task for OCT [82] (even when confocally enhancing the OCT technique [83]), since such paint structures are usually designed to achieve a high level of opaqueness to efficiently hide the underlying substrate. The addition of diverse, highly scattering filler materials (like, e.g., SiO2 particles acting as matting agent or wax particles as forming aids) beside the standard pigments render the situation worse, even for thin paint layer thicknesses of around 10–20 μm. Therefore, usually only topmost and rather transparent clear coatings can be monitored, although approaches, e.g., speckle noise reduction by angular compounding, were introduced in order to improve the detection of interfaces of paint layers [84].
Further public reports on thickness measurements include the evaluation of thin (∼1–3 μm) encapsulation/protection layers for printed organic electronics, which are needed to avoid degradation of the devices by exposure to the ambient (oxygen, humidity) [56, 85], the evaluation of roll-to-roll coated polymer solar cell structures [86]), or of paint layers on stained glass [79]. Thickness measurements were also performed on glass substrates covered by indium tin oxide (ITO) conducting glass (together with the distribution of refractive index and transmission coefficient) [87] as well as quantitative phase imaging to determine the thickness of structured 300 nm ITO films [88]. Evaluation of thicknesses and defects of liquid crystal display (LCD) multilayer structures were equally reported [89], as well as the determination of inner gap distances of individual red-green-blue (RGB) LCD pixels, together with an evaluation of spectral information (absorbance of R,G,B pixels), defects, and the cover glass thickness [90].
Other examples of industrially relevant applications for OCT or OCT-like sensors in thickness evaluation encompass the characterization of loudspeaker membranes, of skins for dry-aged sausages, or of adhesive layers between stacked sensor structures deposited on glass substrates as well as of thin polymer layers deposited on drug-eluting stents.
On-axis thickness evaluations of multiple optical elements and whole optical systems were reported [91], as well as a fully developed application for automated contact lens metrology: the thickness and prism, which is the maximum difference in thickness over the full azimuth at a fixed distance from the edge of the lens, is automatically measured and evaluated using refraction correction and image processing/segmentation [92].
Besides rather planar structures, the evaluation of coating thicknesses and diameter of optical fibers with FD-OCT was demonstrated [93]. Coating thickness measurements of pharmaceutical tablets (deposited, e.g., by drum spray coating) prove to be a further promising application [94–96] for OCT and to be more accurate than indirect methods, like measuring the gain in weight or diameter of the tablets. A similar geometry is experienced when determining the thickness of the so-called nacre layer of pearls produced by oysters around an artificially inserted nucleus, as demonstrated in [97, 98], leading to automated thickness evaluation [99] and dedicated commercial systems for this task.
83.3.3 Imaging of Inner Structures
Besides focusing solely on the surface and on the thickness of covering layers, imaging of the interior of scattering materials is more in-line with the original motivation of OCT and used in NDT to evaluate and verify inner structures and geometries, which can be introduced in an intended way or represent flaws and defects. Naturally, when measuring the thickness of overlaying (multi-)layers, the simultaneous detection of such embedded features is at hand (and also mentioned in nearly all references from the above section), including defects in ITO glass [87], structures and defects in LCD devices [89, 90], bad contact areas between protective coatings and printed electronics substrates [85], or delaminated and misfolded regions of multilayer foil structures [100]. Real-time imaging of chip-type light-emitting devices (LEDs) shall also be mentioned, featuring inspection tasks with respect to correct wire interconnections as well as with respect to the volume and status of the included fluorophore material [101].
In context to the example of pearl investigations of the above section, hierarchical structures built during the nacre formation [98] and a variety of additional aspects could be determined by means of depth-resolved OCT imaging in order to classify pearls, namely, the distinction between bead-nucleated and non-bead-nucleated ones as well as the identification of the type of nucleus used in the pearl production (e.g., freshwater shell or giant clam nuclei) [102]. These studies were further driven and used to distinguish between different types of pearls and pearl treatments (like bleaching, buffing, coating, filling (with epoxy) or dyeing), also by combining OCT with simultaneously performed laser-induced fluorescence (LIF) measurements [103] as exemplified in Fig. 83.4: besides the nacre thickness, the fine structure of the layer as well as the inner features of the nucleus can be determined and used together with the characteristic spectral fingerprint from LIF for nondestructive pearl evaluation.
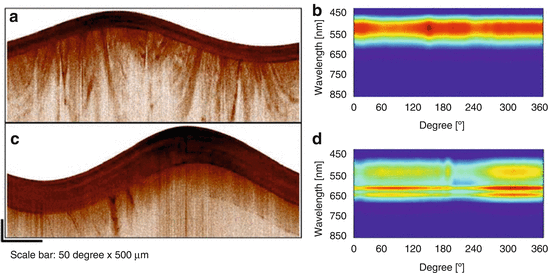
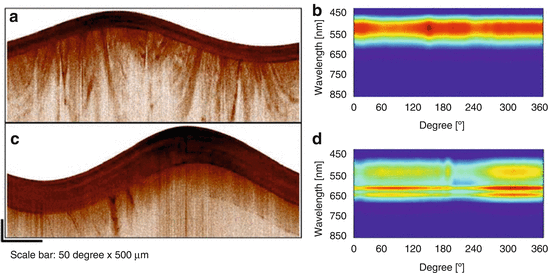
Fig. 83.4
OCT cross-sections (azimuthal scans) of an Akoya (a) and Tahitian (c) pearl. Corresponding LIF spectra (b, d) of the pearls simultaneously measured during OCT acquisition (Reprinted after: M. J. Ju, S. J. Lee, Y. Kim, J. G. Shin, H. Y. Kim, Y. Lim, Y. Yasuno, and B. H. Lee, “Multimodal analysis of pearls and pearl treatments by using optical coherence tomography and fluorescence spectroscopy,” Opt. Express, vol. 19, p. 6420, 2011, with permission from the Optical Society of America © 2011)
Staying with the examples of precious or unique specimens by OCT, the evaluation of jade objects shall be treated: originally introduced to study the subsurface structure in order to distinguish between naturally whitened and artificially treated ones (i.e., by burning) to detect forgery of ancient jade objects [104], further studies followed, especially in hindsight for the classification of diverse types of jade by evaluating the texture and – due to the high penetration depth of several millimeters – to give a guide for artistic carving (i.e., to avoid internal cracks and non-jade inclusions) [105]. Crack structures (linear ones which are open to the air versus cloudy clusters and networks sealed off from the surface) were further investigated for jade materials and classified in detail (inclination, depth, crack initiation sites, etc.) [106]. In the same study, the investigations were also extended towards the characterization of crack morphologies in (ancient) ceramic glaze layers. In general, investigations of glaze layers were among the first applications for art diagnosis [34], and especially by studying the subsurface structure, as performed, e.g., in detail on ancient Egyptian faience [107] or Chinese glazes [108], OCT can help to identify the type of ceramics and provide valuable insight to the production techniques formerly used. Similarly, art conservation studies of historic glass, especially for the imaging of corrosion layers on stained glass or the diagnosis for crizzling (i.e., a network of fine cracking caused by an imbalance of the ingredients and reducing the transparency), have been performed [109]. But not only for ancient glasses has OCT proved to be a promising NDT tool: the investigation of laser-induced damage sites in costly large-aperture optical components has been suggested [110] which could be used in the future to monitor post-processing procedures for damage mitigation [111]. Besides imaging unwanted subsurface features (like cracks and voids induced by laser damage), the verification of intently introduced structures is of interest, as shown for femtosecond laser structuring of fused silica [112] and glass with, e.g., an embedded laser-written waveguide coupler [113]. In case that data is written inside a material, OCT can be used for reliable data retrieval, as, e.g., demonstrated with FF-OCT on 3D laser-structured sol-gels [114] or for multilayer optical discs with OCDR [115].
Bulk ceramic parts and ceramic layers are widely used, e.g., for high-strength hybrid bearings or as thermal barrier coatings protecting blades in gas turbine engines. However, the performance of these materials is crucially dependent on surface and subsurface defects, like cracks in the material itself or delaminations between ceramic layer and substrate, with an early study for subsurface detection of cracks in such scattering ceramic materials, like silicon nitride given in [4]. The evaluation of layered structures in piezoelectric transducer (PZT) composite ceramics and defects in silicon carbide followed [5, 116] with a detailed study of the geometry of so-called Hertzian cracks in silicon nitride balls as used for bearings [117]. In this context, also a comparative study for optical NDT methods (with confocal microscopy and laser backscatter measurements) on subsurface flaws in silicon nitride ceramics was performed [118]. However, one has to state that due to the high scattering nature of such ceramic materials, the imaging depth is significantly restricted: as an example thermal barrier coatings (e.g., yttria-stabilized zirconia (YSZ) coatings for gas turbine engines) were evaluated with OCT to find a new inspection method for monitoring their condition and predicting failure (i.e., spallation). Imaging with wavelengths below 1 μm resulted in penetration depths of less than 300 μm but only for electron beam physical vapor deposition (EB-PVD) coatings. In case of air plasma-sprayed coatings [119], which exhibit a far more scattering structure than the columnar one of EB-PVD, the imaging depth is further reduced [120]. Similarly, a limited penetration depth around 260 μm was found even for the 1.3 μm spectral range when imaging alumina-based ceramics which are used, e.g., as inert container material for microfluidic structures: the geometry of embedded channels, cavities, the position of metal stripes (electrodes) and again the detection of defects as well as the thickness determination of covering layers and roughness were the origin of interest in these studies [121, 122]. Additionally, Monte Carlo simulations were performed to predict the performance of OCT for depth-resolved imaging depending upon the optical/scattering parameters of these materials. Finally, in the context of ceramic materials, the evaluation of domain boundaries in periodically poled ferroelectrics shall be mentioned: the (unwanted) refractive index changes near the anti-parallel domain walls, which are in the order of 10−4, could successfully be traced [123].
Regarding pronounced scattering, the multiple interfaces between fibers and air or between fibers and embedded fillers play a similar role as the grainy and porous structure of most ceramic materials presented above. Consequently, structural imaging of fibrous networks like paper is also for OCT a challenging task, as already seen for the thickness measurements presented in the prior section. Nevertheless, useful information can be extracted by, e.g., studying larger-scale paper simulation networks; insight on the filler content can be obtained by evaluating the slope of the backscattered depth profile signal [76]; or the degree of paper porosity can be deduced from OCT measurements when compared with Monte Carlo simulations [124]. Similar challenges in coping with scattering have to be met for the characterization of, e.g., electro-spun polymer fiber web structures [125]. However, when transparent fiber structures are embedded in a homogenous medium, OCT imaging with penetration depths of even several millimeters is easily accomplished (especially at wavelengths around 1,550 nm [126]), with glass fiber-reinforced polymer (GFRP) composites as prominent examples shown in Fig. 83.5: novel, knitted glass fiber fabrics embedded in an epoxy matrix and exhibiting improved mechanical properties were investigated by ultrahigh resolution (UHR) OCT [127]. In contrast, for carbon fiber composites (CFCs), usually only the surface structure can be evaluated due to the strong absorption of the fibers [100], which is also valid, e.g., for carbon nanotubes (CNTs) as filler materials in epoxy resin, as shown in a recent study to clarify the effect of plasma treatment on the dispersion of the CNTs in the matrix [128].
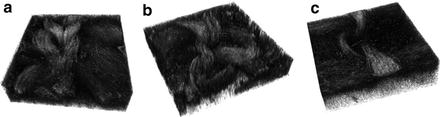
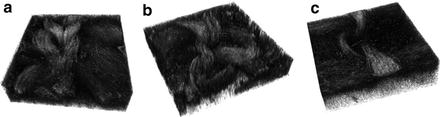
Fig. 83.5
3D data sets of knitted GFRP structures (scan areas: (a, b) 5 × 5 mm2, (c) 3 × 3 mm2; thickness of displayed stacks: 300 μm) (Reprinted from Comp. Sci. Technol. vol. 67, p. 3051, 2007, K. Wiesauer, M. Pircher, E. Götzinger, C. K. Hitzenberger, R. Oster, and D. Stifter, “Investigation of glass–fibre reinforced polymers by polarisation-sensitive, ultra-high resolution optical coherence tomography: Internal structures, defects and stress”, with permission from Elsevier © 2007)
Depth-resolved imaging tasks in material research for OCT in the context of the evaluation of GFRPs can be found for the prediction of mechanical properties by acquiring the internal structure but are also concerned with the detection and classification of defects like cracks, kink bands, fiber matrix de-bonding, voids, dry spots, and large-scale delaminated areas [129], as also shown in comparison with other NDT methods like X-CT and confocal microscopy [130]. Equally, the permeability of the fiber structure for infiltration with the liquid epoxy matrix material was predicted by image-processed OCT cross-sections [131]. Concerning the visibility of the glass fiber structure, it has to be noted that there is improved contrast when rather low-refractive-index matrix materials are used [132] and that high resolution or even better UHR-imaging is of advantage when not only whole fiber bundles but individual fibers should be resolved [127]. In the case of short fiber-filled polymer composites, resolving the individual fiber pieces is essential for the determination of the fiber orientation which influences the isotropy of mechanical properties: by advanced image processing algorithms, the fiber orientation was automatically deduced from UHR-FF-OCT images and verified with micro X-CT [133]. Other types of polymer composites are equally promising for OCT imaging due to their translucent nature, with one example of OCT being used to study thermal degradation effects in microsphere filled polymers [134]. Another task in the development of novel polymer materials, which have to meet increasing performance requirements, e.g., for future automotive applications, is the evaluation of the distribution of different polymer phases in polymer blends, as shown for polypropylene-rubber blends with UHR-OCT, which gave even superior contrast than synchrotron phase-contrast CT [100]. Naturally, when pure bulk polymers without any additional inclusions are present (see also Fig. 83.1), OCT is very promising for the imaging of the structure of whole injection-molded parts [126], of co-extruded polymer panels [100], or of polymer foams [67].
As example for natural composites, wooden specimens are worth to be mentioned, with an instructive study given in [135] where the structure of the wood fibers was successfully imaged with a FF-OCT for an eighteenth-century violin below (transparent) ground paint and varnish layers. This application leads us further to the evaluation of other natural materials like the detection of subsurface features in melon seeds hinting at a virus disease [136], imaging of major structures within tomato seeds [137], or hull thickness determination of lupin seeds by OCT as a novel screening method to classify different genotypes with respect to the de-hulling abilities or nutritional aspects [138]. To study selected aspects of food can be helpful for quality control (screening of internal defects and rots in onion bulbs [139]) as well as for food engineering and storage, with the evaluation of the microstructure of cereals (swelling and rehydration behavior when exposed to liquids) and the investigation of lenticels (i.e., pores for gas exchange) and wax layer of apples as recently introduced examples [140]. Finally, protein crystals were imaged and the structure compared to those of salt crystals in order to facilitate automated sorting in the future [141].
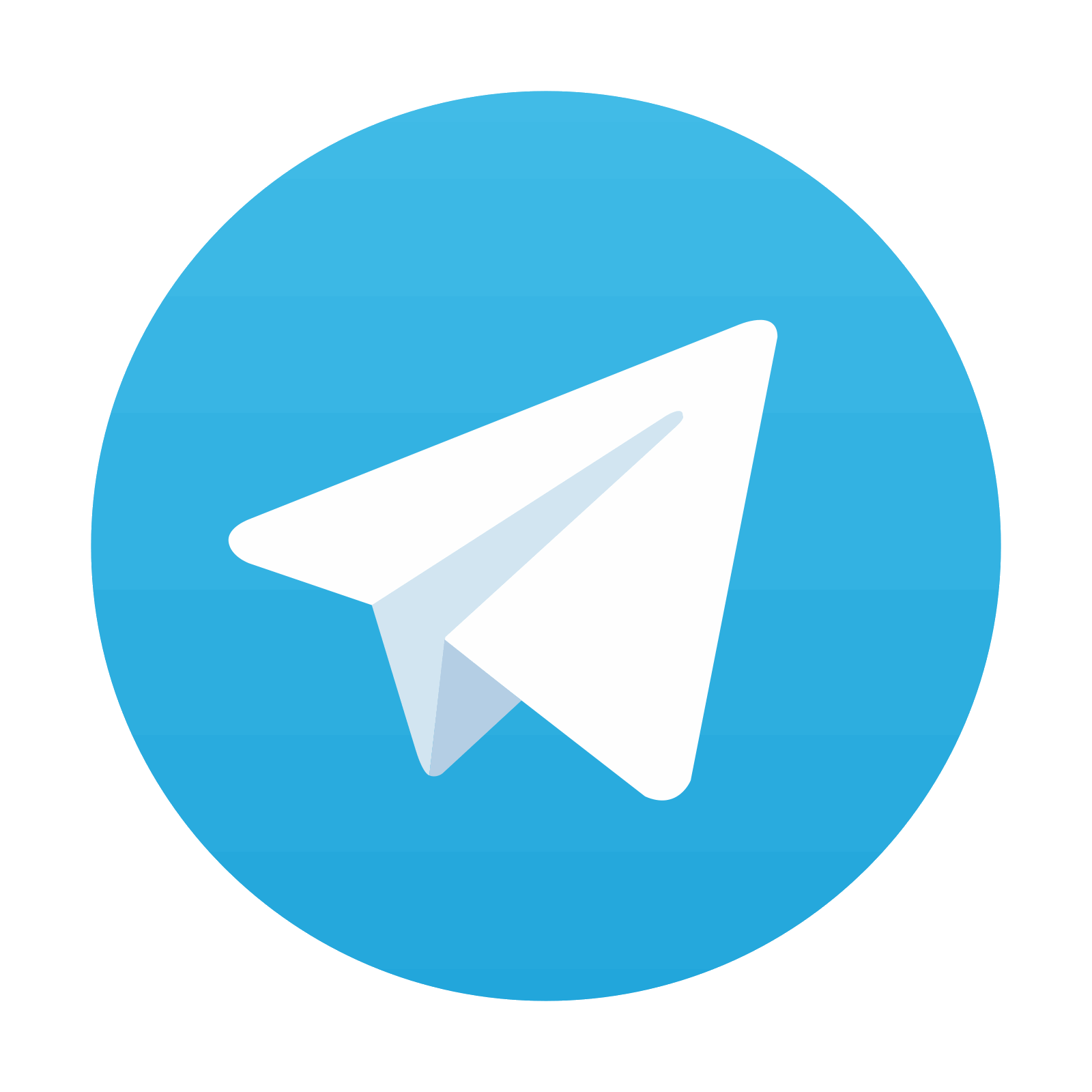
Stay updated, free articles. Join our Telegram channel
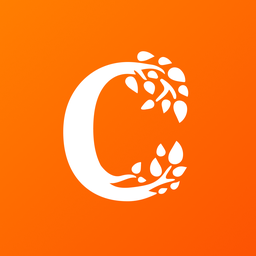
Full access? Get Clinical Tree
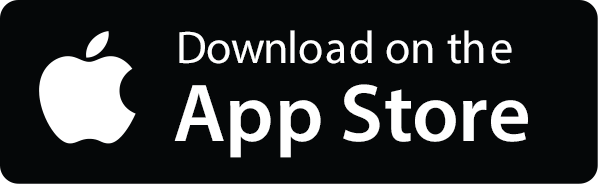
