Spectacle Lens Materials
Gregory L. Stephens
Darryl J. Meister
Since the 1960s, the use of plastic as a spectacle lens material has increased dramatically. During this same time period, domestic lens shipments of glass lenses by U.S. manufacturers have decreased from a dominant position to about 1% of the ophthalmic lens market, and much of the glass lens market consists of photochromic products. A relatively recent trend has been the increased use of mid-index and high-index lens materials, materials with indices of refraction higher than that of CR-39 plastic or crown glass. These materials have now captured almost one-half of the spectacle lens market, and the most popular material, polycarbonate, accounts for approximately ¾ of all high-index plastic lenses sold.1 In some markets the use of polycarbonate approaches that of CR-39.
What are the properties of a high-quality spectacle lens? First, the lens must be highly transparent and have good optical quality. All lens materials are transparent, and proper lens design provides most lenses with the proper off-axis optical quality. However, transverse chromatic aberration can be a problem for high-power, high-index lenses. Second, the lens should be thin and lightweight. Eyewear consumers want lenses that are thin and light; high-index plastics provide the best match to these requirements. Third, a lens should be scratch-resistant. Although glass is the most scratch-resistant of all lens materials, manufacturers of plastic lenses have developed scratch-resistant coatings that in most cases last for the life of the lens. Fourth, the lens should be impact-resistant. Almost all spectacle lenses can be manufactured to meet FDA-mandated impact-resistance requirements, but polycarbonate and Trivex provide exceptional impact resistance and eye protection when compared to all other materials. Fifth, lens materials should be easy for optical laboratory personnel to surface, edge, drill, and tint. Ease of processing varies considerably among materials, and some materials will have advantages for specific spectacle frame types. Finally, a lens material must be affordable. Lens materials vary widely in cost. CR-39 plastic, crown glass, and polycarbonate plastic are at the low end of the price scale, whereas mid-index and high-index plastics (other than polycarbonate) are the more expensive “premium” lens materials.
Table 1 lists physical properties of representative plastic and glass spectacle lens materials and compares these materials for the properties just mentioned. This chapter provides further information on lens materials, with an emphasis on lens design, cosmetic appearance, and impact resistance.
Table 1 Representative Plastic and Glass Lens Materials | ||||||||||||||||||||||||||||||||||||||||||||||||||||||||||||||||||||||||||||||||||||||||||||||||||||||||||||||||||||||||||||||
---|---|---|---|---|---|---|---|---|---|---|---|---|---|---|---|---|---|---|---|---|---|---|---|---|---|---|---|---|---|---|---|---|---|---|---|---|---|---|---|---|---|---|---|---|---|---|---|---|---|---|---|---|---|---|---|---|---|---|---|---|---|---|---|---|---|---|---|---|---|---|---|---|---|---|---|---|---|---|---|---|---|---|---|---|---|---|---|---|---|---|---|---|---|---|---|---|---|---|---|---|---|---|---|---|---|---|---|---|---|---|---|---|---|---|---|---|---|---|---|---|---|---|---|---|---|---|
|
Plastic Lens Materials
All plastic spectacle lens materials are polymers, long-chain molecules with repeating subunits. These molecules can have considerable cross-linking, and the amount of cross-linking influences the properties of the material, most notably impact resistance and tensile strength. Plastic lens materials are commonly divided into three categories.2 Thermosetting plastics have large amounts of cross-linking. CR-39 and all of the high-index plastics except polycarbonate and Trivex have this structure. Thermosetting plastics all have acceptable but not extreme impact resistance and are manufactured in a similar manner. Thermoplastics have little cross-linking. The molecules of thermoplastics can slide back and forth easily on each other. The result is a tough material that can be flexed and even permanently deformed without breaking. The best example is polycarbonate. The energy of an impact tends to flex or deform a polycarbonate lens rather than break it. This property results in extremely high-impact resistance. However, the surfaces of a polycarbonate lens are very soft, and the surfaces must have scratch-resistant coatings. Trivex, also known as Trilogy (Younger Optics, Torrance, CA) and Phoenix (Hoya Vision Care, Americas, Lewisville, TX) has a molecular structure in-between that of polycarbonate and CR-39 and can be termed a quasi-thermosetting plastic. It consists of long-chain molecules but with an intermediate amount of cross-linking. Trivex is extremely impact-resistant, but is not as easily scratched as polycarbonate.
CR-39 Plastic
CR-39 (PPG Industries, Pittsburgh, PA) is the standard ophthalmic plastic currently in use. Also known as allyl diglycol carbonate or allyl resin, CR-39 was developed during World War II.3 Robert Graham and associates, of Armorlite Optical, discovered a practical method for manufacturing lenses from CR-39 using glass molds.4 For many years, CR-39 had only a minor role in the optical industry, but in the late 1960s and early 1970s, as frame styles became larger and weight became a more important concern, the use of CR-39 began to increase. Today, CR-39 plastic lenses make up approximately one-half of domestic lens shipments by U.S. manufacturers.1
CR-39 has the lowest index of refraction of all currently used spectacle lens materials, so lenses made of CR-39 are thicker than those made from other materials. However, CR-39 has approximately one-half the density of the standard spectacle lens glass, ophthalmic crown, so CR-39 lenses are about one-half the weight of glass.
Factory-finished stock CR-39 lens blanks are cast in glass molds separated by rubber-like gaskets to provide the required thickness. The material has a shrinkage factor of approximately 14% during the casting process. This shrinkage alters the lens curves and changes the tangential and sagittal errors from their expected values. This is not a serious problem, but tables of predicted off-axis performance as a function of base curve for finished stock lenses should not be used for comparing the performance of lenses from different manufacturers.
Semifinished CR-39 plastic single-vision and multifocal blanks are not affected significantly by shrinkage during the casting process because the blanks are kept to a more uniform thickness than is possible with finished lenses and the shrinkage does not modify the spherical surfaces. The second surface is ground and polished in the optical laboratory. Off-axis performance can be predicted by the design base curves. There are only small differences in the theoretical performance between crown glass and ground and polished CR-39 plastic lenses.
Polycarbonate Plastic
Polycarbonate is a high-index plastic, a lens material with an index of refraction higher than that of either CR-39 plastic or crown glass. Originally developed in 1953 by Daniel Fox of General Electric, polycarbonate has exceptional impact resistance and has been used in everything from astronaut helmets to cell phones, compact disks, and automobile parts.5 The original ophthalmic use for polycarbonate was industrial eyewear. Polycarbonate has continued to be a popular lens material for everyday (dress) eyewear because of concerns about eye protection and because the high index of refraction of polycarbonate results in relatively thin and light lenses.
The radius of curvature of a lens surface is related to its power by:

where n and n’ are the indices of refraction before and after refraction at the surface, respectively, r is the radius of curvature of the surface, measured in meters, and F is the surface power in diopters. The difference in radius of curvature between the front and back surfaces for a high-power lens is relatively large for a lens made from a low-index material such as CR-39 plastic or crown glass. Because the surface radii differ, there must be a relatively large difference between the center thickness and the edge thickness of the lens. A high-index material such as polycarbonate decreases lens thickness by decreasing the difference in radius of curvature between the two surfaces. The edge thickness of a minus-power lens or the center thickness of a plus-power lens (above the necessary minimum center thickness value) is inversely related to its index of refraction.
Figure 1 shows cross-sectional views of CR-39 plastic and polycarbonate lenses of powers +5.00 D and -5.00 D. The center thickness of the + 5.00 D polycarbonate lens is approximately 10% less than that of the CR-39 plastic lens of the same power. The edge thickness of the -5.00 D polycarbonate lens is approximately 20% less than that of the CR-39 plastic lens of the same power. Aspheric lens designs can provide additional decreases in thickness.
Polycarbonate has a market share approaching that of CR-39. With the increased market share has come decreased cost, so polycarbonate is considered to be a “value” material. A polycarbonate lens is thin and light, in part because of its increased index of refraction and low density, but also because the impact resistance of polycarbonate allows a lens of minus power to have a center thickness as low as 1.0 mm. Polycarbonate is available in most lens types, including single-vision, aspheric, bifocal, trifocal, and progressive addition lenses. Again, this reflects the large market share of polycarbonate. Dispensers are more likely to use materials that they can obtain easily from their optical laboratory.
Polycarbonate must be molded in large presses under pressures of several thousand pounds per square inch for the more common prescriptions, and surfacing and edging often require special procedures. A manufacturer wanting to enter the high-index lens market can do so much more cheaply with a material other than polycarbonate.
An issue with polycarbonate is its rather large amount of chromatic dispersion and transverse chromatic aberration, which patients with high-power prescriptions may notice as blur or color fringes around objects as they looks away from the centers of their lenses. This topic will be discussed in detail in a later section.
Mid-Index and High-Index Plastics (Other Than Polycarbonate)
High-index materials other than polycarbonate continue to increase in market share, as well. These materials are often further divided into two subcategories, “mid-index” materials with indices from 1.53 to 1.59, and “high-index” materials with indices of 1.60 and higher. The highest index currently available commercially in the United States is approximately 1.74, but research continues on the development of materials of even higher index. Mid-index and high-index lens materials are often combined with aspheric designs and decreased center thickness (in minus powers) in order to provide additional reductions in lens thickness and weight.
The most popular of the mid-index and high-index plastics are arguably lens materials with indices of 1.60 and 1.66 (or 1.67, depending upon the reference wavelength). A number of popular polymers (e.g., MR-6, MR-7, MR-8, and MR-10), each with slightly different properties, are available (Table 1). The trend is toward decreased use of the mid-index materials, except for Trivex, which has an impact resistance similar to that of polycarbonate. High-index lens materials typically have significant dispersion, which can create problems with transverse chromatic aberration with off-axis viewing, particularly in higher prescriptions. Mid-index materials provide a balance between off-axis optical quality and thickness. Trivex presents a good example. Trivex has fewer color aberrations than polycarbonate and other high-index materials, but its relatively low index (1.53) will result in thicker lenses relative to these materials at the same minimum thickness. Trivex can be made, however, with a 1.0 mm center thickness in minus powers and also in aspheric designs, which can decrease thickness considerably in moderate prescription powers. Because Trivex is just as impact-resistant as polycarbonate, only polycarbonate or Trivex should be used when impact resistance and eye safety are concerns.
Mid-index and high-index lens materials other than polycarbonate are surfaced and edged in a manner similar to that of CR-39 plastic. Lens materials with indices of 1.60 and above, commonly termed polyurethane plastics, contain sulfur and aromatic hydrocarbons. These materials have a characteristic unpleasant smell when surfaced and edged.
Glass Lens Materials
Ophthalmic Crown Glass
Standard ophthalmic crown glass is a mixture of sand (silicon dioxide), soda (Na2O), and lime (CaO). These materials are combined under high heat, resulting in a glass that has a random amorphous structure. Attractions between atoms or ions of the glass create bonds that are inherently extremely strong. However, even the slightest imperfection in a lens surface, such as the abrasion caused by rubbing with paper or a small defect caused by rough handling, weakens a brittle material like glass. The low index of refraction and relatively high density of crown glass results in thick, heavy lenses at high powers, and its usage has decreased greatly.
High-Index Glass
A few high-index glass lens materials exist, although none are commonly used. Most contain oxides of metals such as titanium, lanthanum, or niobium as additives to increase the index of refraction. High-index glass lens materials are denser than crown glass and have more chromatic dispersion. The increased index of refraction decreases lens thickness, but the increased density tends to offset any weight advantage relative to crown glass. High-power lenses made of high-index glass are usually too heavy for comfortable wear unless the frame is fitted carefully to the patient’s nose and ears. The increased chromatic dispersion requires that the effects of off-axis chromatic aberration be considered for higher powers.
Probably the most commonly used of the high-index glass lens materials is the titanium oxide glass High-Lite 1.7. Lens materials with indices as high as 1.90 are manufactured, but these materials are not distributed in the United States because lenses will not meet FDA impact resistance requirements. Because of liability considerations, it is difficult to justify ever prescribing for cosmetic reasons (i.e., to make the lenses thinner) a material that is not impact-resistant. The use of these extremely high-index materials cannot be recommended.
Flint glass is an older type of high-index glass made by adding lead oxide to the standard glass mixture. It is used only for such applications as x-ray protection for technicians in a hospital setting. Flint glass cannot be tempered to increase its impact resistance to acceptable levels. When flint glass or other nonimpact-resistant materials are prescribed, the FDA requires that the patient be notified in writing that the lenses are not impact-resistant.6
Lens Materials and Chromatic Aberration
White light is made up of a number of different wavelengths. These wavelengths travel at different velocities through transparent materials, which means that the index of refraction varies as a function of the wavelength or color of light. Blue light has a higher refractive index- and undergoes more refraction- than red, resulting in chromatic dispersion (Fig. 2). The degradation of image quality that occurs in an optical system as a result of dispersion is chromatic aberration.
The ophthalmic industry quantifies the dispersion of a lens material using the Abbe number (νd), defined as follows:7

where nd is the index of refraction of the lens material for yellow light of wavelength 587.56 nm (the helium d line), nF is the index for blue light of wavelength of 486.13 nm (the Fraunhofer F line), and nC is the index for red light of wavelength of 656.27 nm (the Fraunhofer C line). The degradation of image quality that occurs as a result of dispersion is chromatic aberration. Consequently, lens materials with higher Abbe numbers have less chromatic dispersion and are less likely to cause problems with chromatic aberration. As a general rule, the Abbe number tends to decrease as index of refraction increases (Table 1), so materials of higher index have more chromatic dispersion than lower index materials.
A simple formula relates the amount of transverse chromatic aberration at a given point on a lens to its power and Abbe number:8

where h is the distance of the point from the optical center, measured in centimeters, F is the lens power in diopters, and νd is the Abbe number. Transverse chromatic aberration has units of prism diopters because the term h × F is Prentice’s rule, the formula for calculating the amount of prism at any point on a lens. Equation 3 shows that transverse chromatic aberration can only be a problem when a patient looks through a point that is off-axis (away from the lens center), when the lens is of relatively high power, and when the lens has a high index of refraction (when the Abbe number is low).
Both theoretical and experimental studies of transverse chromatic aberration suggest that the threshold for its detection is approximately 0.10 prism diopters.9,10 With this information, the lens power at which transverse chromatic aberration should be detectable can be calculated from equation 3. Polycarbonate, a high-index material with an Abbe number of 30, will be used as an example. At a distance of 1.5 cm (approximately 30 degrees) from the optic axis, the threshold of 0.10 prism diopters of transverse chromatic aberration is reached for a lens power of 2.00 D. Yet, clinical experience suggests that patients do not report problems caused by the chromatic aberrations of polycarbonate for lens powers less than approximately ±5.00 D. Even then, many patients are willing to tolerate its effects because a high-index material results in such thin and light lenses.
The difference between theory and clinical experience is probably related to the differential effects of transverse chromatic aberration on high- and low-contrast objects. When any object is viewed through a lens with transverse chromatic aberration, the color fringes only blur the target in one meridian, with other meridians relatively unaffected. For a high-contrast object, this blur might not be expected to have much effect on visual acuity because the other meridians are still in focus. However, in low-contrast situations, transverse chromatic aberration may be more of a problem because even the unaffected meridians of the object are difficult to resolve. In other words, transverse chromatic aberration lowers retinal image contrast in both the high- and low-contrast situations, but the contrast loss in the low-contrast situation may be more critical for visual resolution.
The likelihood of patient dissatisfaction as a result of chromatic dispersion can be minimized by selecting lens materials with higher Abbe numbers. Fortunately, many high-index materials are now available with relatively high Abbe numbers. Further, although the chromatic dispersion of a given high-index lens material cannot be eliminated, it is possible to minimize its effects on a patient’s vision by proper selection and positioning of lenses in the optical dispensary. Probably most important is proper vertical positioning of the optical centers of the lenses. Because transverse chromatic aberration is proportional to the distance from the optic axis of the lens, ensuring that the optical centers are located in front of the wearer’s lines of sight during primary (straight-ahead) gaze will significantly ameliorate the effects of chromatic dispersion- at least when prism has not been prescribed.
The optical centers are correctly positioned horizontally by taking accurate interpupillary distance (PD) measurements with a pupillometer. It is also possible to supply the optical laboratory with pupil height measurements to vertically position the optical centers; otherwise the optical centers are usually positioned by the optical laboratory along the horizontal midline (or datum line) of the frame. Split or monocular PDs should be provided to the optical laboratory by the dispenser whenever high-power, high-index lenses are ordered. Specifying a vertical position for the optical centers can increase the thickness and weight of the lenses, however, which can compromise the benefits of high-index materials. Ensuring that the patient chooses a frame that leaves his or her eyes well-centered and close the midline of the frame is preferable to vertically positioning the optical centers.
The off-axis optical quality of a spectacle lens is best when the optic axis of the lens passes through the center of rotation of the eye. This optic axis position tends to minimize off-axis monochromatic aberrations. As a rule-of-thumb, the optic axis of a lens will pass vertically through the center of rotation of the eye if the optical center of the lens is dropped 1 mm below the center of the patient’s pupil for every 2 degrees of pantoscopic tilt. Because most frames have roughly 6 to 10 degrees of pantoscopic tilt, the optical center should be positioned 3 to 5 mm below the pupil center as the patient looks straight-ahead. This is close to the normal optical center position for most well-fit frames, but the dispenser can order spectacles with a specified vertical optical center position relative to the bottom of the patient’s lenses when necessary. Additionally, a close-fitting frame with a short vertex distance will minimize the amount of transverse chromatic aberration introduced at any angle of gaze by reducing the “h” value in equation 3.
It can be argued that the blur a patient notices when looking off-axis is a combination of all of the available aberrations. By minimizing the effects of monochromatic aberrations, the patient may therefore be less likely to notice the chromatic aberrations. Proper base curve selection will ensure that off-axis visual quality is maximized, so the manufacturer’s recommended base curve should generally be used for each prescription; that is, the base curve should match that recommended on a base curve chart. Some manufacturers may use smaller base curve steps for their high-index lens series to provide better control of monochromatic aberrations.
To summarize, careful positioning of the optical centers, both vertically and horizontally, is necessary for patients wearing high-power, high-index spectacle lenses. These are the same measurements that should be made for patients wearing aspheric and atoric lens designs, although a well-fitting frame that does not require a change to the vertical position of the optical centers may achieve a better cosmetic result. Proper base curve selection provides optimal off-axis aberration correction so that the patient is less likely to notice off-axis blur.
Thickness, Weight, and Cosmetic Appearance
Cosmetic appearance is the driving force in the spectacle lens marketplace today, not the optical quality of the lens. Patients want lenses that are thin and light, and plastic high-index lens materials provide these properties.
Lens Thickness
The thickness of a spectacle lens is determined by two main parameters, the lens power and the lens size. For a given minimum center thickness, the edge thickness of a minus-power lens will increase as the power increases and as the lens or frame size increases. The center thickness of a plus-power lens of given minimum edge thickness will increase as power increases and as lens size increases. As rules-of-thumb, the edge thickness of a minus-power lens or the center thickness of a plus-power lens is directly proportional to the lens power and also directly proportional to the square of the diameter of the minimum blank size needed to make the lens. Therefore, the simplest way to decrease lens thickness is to use frames with small eyesizes.
Increasing the index of refraction also decreases edge thickness for a minus-power lens and decreases center thickness for a plus-power lens. It is possible to calculate edge thickness and center thickness values for a lens of given size, power, and index, but simple rules-of-thumb are available for the most common materials. For example, a polycarbonate lens or a 1.60 index lens will be approximately 20% thinner than a CR-39 lens of the same size and power. A lens of index 1.67 can be up to 30% thinner than a CR-39 lens, whereas a lens of index 1.74 can be about 40% thinner.
Aspheric lens designs decrease edge thickness for a minus-power lens and decrease center thickness for a plus-power lens. This effect is mainly the result of the flatter base curve of aspheric designs, although the aspheric curve shape itself also provides a slight thickness reduction. The flatter base curve provides further improvements in the cosmetic appearance of plus-power lenses by decreasing magnification and decreasing the distance that the lenses bulge out the front of the frame. Flatter lenses also tend to fit better into a spectacle frame.
Still another way to decrease the edge thickness of a minus-power lens is to provide the lens with the minimum possible center thickness. The minimum center thickness value that will allow a minus-power CR-39 lens to meet FDA impact resistance requirements is about 1.5 to 2.0 mm. Polycarbonate and Trivex can have a center thickness as low as 1.0 mm, and some of the other mid-index and high-index plastics may also be available with center thicknesses of 1.0 to 1.5 mm. However, a 1.0 mm center thickness lens should be used with caution because it is less impact-resistant than a thicker lens. In addition, a thinner lens may flex when impacted and be more readily dislodged from a spectacle frame than a thicker lens,11,12 possibly causing an eye injury even if the lens does not break. When edge thickness is a critical concern for a minus-power lens, an aspheric design with a 1.5-mm center thickness can provide an edge thickness similar to that of a spherical design with a 1.0 mm center thickness but with improved impact resistance. Polycarbonate or Trivex with a center thickness of either 2.0 or 3.0 mm is best when impact resistance is a significant concern.
The center thickness or edge thickness of a finished, edged minus-power lens does not depend upon the size of the lens blank used to make it. Using a lens blank that is too large is just more expensive and wasteful of lens material. However, the center thickness or edge thickness of a finished, edged, plus-power lens is dependent on the blank size used. Larger plus-power lens blanks have thicker centers, so using a lens blank that is too large results in a lens that will have a thicker center than desired. This lens will also have a thicker than desired edge. The best strategy for making plus-power lenses is to always use the smallest lens blank available. If a small blank is not available, then the optical laboratory should make a small blank by surfacing a semi-finished blank to the thickness required. As center thickness decreases during surfacing, the blank size will also decrease.
Lens Weight
The weight of a spectacle lens will be related to its index of refraction, size, center thickness, and density. The use of high-index plastic materials decreases lens thickness, which also decreases lens volume and weight. Materials that are less dense will also weigh less for a given volume. Most of the high-index plastics have similar densities, although density does tend to increase slightly as index increases (Table 1). Density does not have much effect on lens weight for plastic lens materials.
Table 2 summarizes methods for decreasing the weight and thickness of a patient’s spectacle lenses. In most cases the thinnest, lightest lens is one that is made of a high-index plastic, has a 1.0 mm center thickness (if of minus-power), is in a small frame, and is made with an aspheric design. This combination is commonly available in today’s ophthalmic market.
Table 2 Decreasing the Weight and Thickness of Spectacle Lenses | ||||||||||||
---|---|---|---|---|---|---|---|---|---|---|---|---|
|
Mechanical Properties of Lens Materials
Scratch Resistance
Scratch-resistant coatings or hard coatings increase the scratch resistance of plastic lenses, which are otherwise prone to both fine abrasions from cleaning and deep scratches. Scratches can scatter light, interfere with vision, and even compromise the structural integrity of a lens. A scratch-resistant coating may be applied to a lens by either the lens manufacturer or the optical laboratory. Many manufacturer-applied coatings are spin coatings.13 A small amount of the coating material is applied to the center of the lens surface as the lens spins at a controlled rate. The coating material then spreads out to cover the lens surface. Others manufacturer-applied coatings are dip coatings, where the lens is dipped into the coating material, then removed at a constant rate to control the thickness.13 Some coatings may even be in-the mold coatings, where the inside of the lens mold is coated with the coating resin. The coating is partially cured before the liquid lens material is added to the mold.14 Coatings applied by lens manufacturers are generally high-quality coatings that are durable and adhere well to the lens substrate.
Scratch-resistant coatings influence the ability of a plastic lens to accept a tint. As a general rule, harder scratch-resistant coatings that are the most difficult to scratch do not tint as well as softer coatings. Many manufacturers sacrifice scratch resistance to improve the tintability of their lenses, so it is usually not productive to compare the quality of scratch-resistant coatings from different manufacturers.
Semi-finished lens blanks with a scratch-resistant coating will be supplied to the optical laboratory with the coating on only the front surface. After surfacing the back surface to the proper power, optical laboratory personnel commonly apply a spin coating that is cured with ultraviolet radiation. This coating is especially important for polycarbonate, which must always have a scratch-resistant coating on both lens surfaces. Laboratory-applied coatings vary in both scratch resistance and tintability and may not be as durable as manufacturer-applied coatings.
Many manufacturers of antireflective coatings now apply thermally cured scratch-resistant coatings made of a durable polysiloxane to a lens surface before the antireflective coating is applied. These coatings, sometimes termed varnishes, can actually improve the durability and scratch resistance of an antireflective coating.
A properly applied scratch-resistant coating must be mechanically compatible with the lens substrate and with any other applied coatings. It is important for a coating and the lens substrate to have similar coefficients of expansion to prevent the coating from delaminating when heated, as might occur if the lenses are left on a car dashboard on a hot, summer day. Also, because scratch-resistant coatings and antireflective coatings are relatively brittle, their application can significantly decrease both the impact resistance and tensile strength of a lens. When a coated lens receives an impact, the brittle coating tends to crack before the more flexible lens substrate. Because the coating is strongly adherent to the substrate, the crack may then propagate throughout the entire lens, breaking it into pieces.
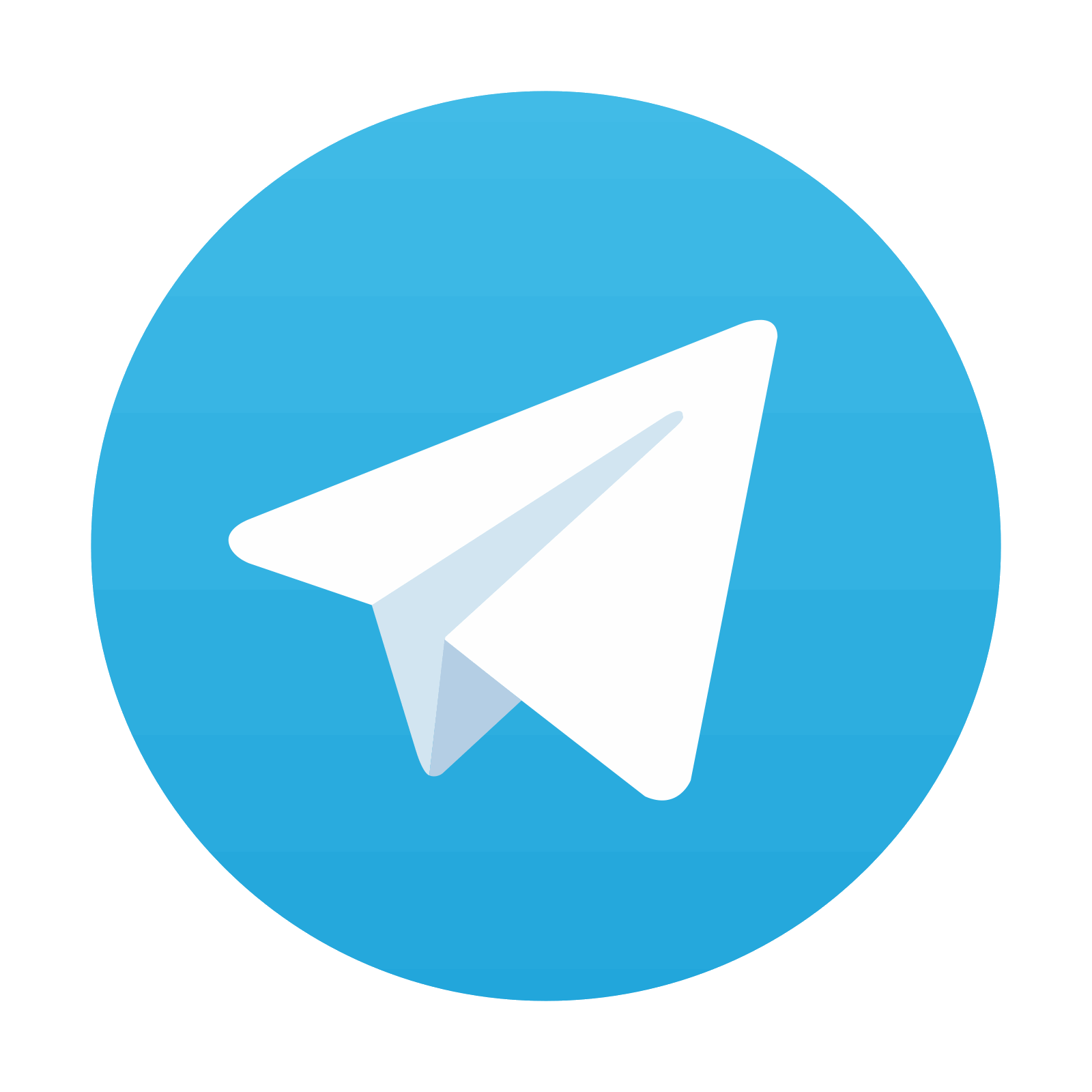
Stay updated, free articles. Join our Telegram channel
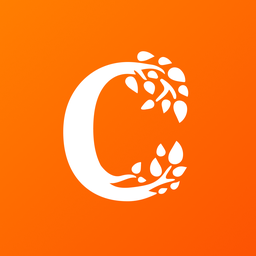
Full access? Get Clinical Tree
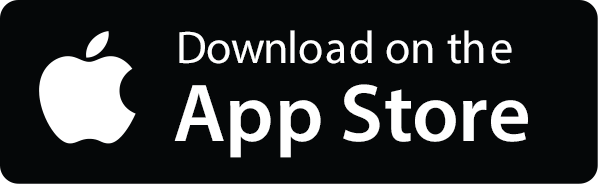
