Introduction
Rigid lens materials have played an important role in the development of rigid contact lenses generally and occupy a small but significant place in the range of currently available products. Much of the relevant information is contained in the patent literature, which is analysed in some detail elsewhere ( ).
Polymethyl Methacrylate
To appreciate the way in which rigid, as distinct from soft, materials have developed, it is necessary to go back to the period following World War II. The new availability of plastics materials, specifically polymethyl methacrylate (commonly known as PMMA), led to the design and development of the first corneal lens as a replacement for glass scleral lenses. The PMMA lenses were prepared by polymerization of methyl methacrylate with a free-radical initiation system ( Fig. 11.1 ) to form rods or buttons from which a lens was obtained by lathing and polishing. Fig. 11.1 represents the assembly of n methyl methacrylate units to form a PMMA chain n units long. PMMA was an ideal candidate for use as a hard contact lens material because it had a similar appearance and ease of fabrication to glass, acceptable surface wettability and excellent durability. The lenses were compared favourably with scleral lenses in that they were thin and lightweight, could be worn more comfortably and gave excellent visual correction.

The Need for Oxygen
By the 1960s a greater appreciation of the effects of contact lens wear on the anterior eye was developing and the fact that PMMA is essentially a barrier to oxygen transport became widely recognized. Corneal physiologists at that time were not only able to carry out theoretical calculations on the effect of contact lenses on corneal respiration but were also able to carry out well-differentiated experiments using PMMA and a very different material, silicone rubber ( Fig. 11.2 ).

Some aspects of the structure and behaviour of polymers, including these two materials, have been outlined in Chapter 4 . The most important property to consider in the context of the present discussion is the difference in their oxygen permeabilities. PMMA is a glassy thermoplastic material, which has advantageous optical clarity, processability and ease of sterilization, but the disadvantage, as a contact lens material, of virtual impermeability to oxygen. Silicone rubber, on the other hand, belongs to a group of materials known as synthetic elastomers, which are not only flexible but also show rubber-like behaviour (i.e. they are capable of being compressed or stretched and when the deforming force is removed they instantaneously return to their original shape). They consist of polymer chains that possess high mobility and are cross-linked at intervals along the polymer backbones. Because of this chain mobility, oxygen is able to diffuse rapidly through the structure. These polymers have oxygen permeabilities more than 100 times greater than that of PMMA. Silicone rubber is the most significant member of the group, with an oxygen permeability around 1000 times greater than that of PMMA. This extremely high oxygen permeability arises from the backbone of alternate silicone and oxygen atoms, which confers not only great freedom of rotation but also a much higher solubility for oxygen than is possessed by rubbery polymers with simple carbon backbones.
Silicone rubber lenses, surface treated to give acceptable wettability, were developed in the mid-1960s ( ) and found clinically to have a little deleterious effect on corneal respiration ( ). The problems of maintaining adequate surface properties, which were initially encountered in its routine clinical use, have never been fully overcome, however, and silicone rubber lenses are used only rarely. The uniquely high oxygen permeability of the silicon–oxygen backbone has, however, been harnessed into two distinct types of contact lens material: silicone hydrogels ( Chapter 4 ) and the so-called rigid gas-permeable materials described here. Because PMMA is now essentially redundant as a contact lens material, the term ‘rigid gas-permeable’ is equally redundant. All rigid lenses manufactured today (aside from PMMA) are gas permeable. For this reason, the term ‘rigid lens’ is used throughout this book and is intended to refer to all rigid lenses apart from PMMA, unless the latter is specifically designated.
The Problem of Hydrophobic Surfaces
Elastomers, such as silicone rubber, are in many ways intermediate between thermoplastics such as PMMA and hydrogels such as poly(hydroxyethyl methacrylate). Thus they possess to a degree the toughness associated with the former group of materials and the softness of the latter, and in this sense, they are ideal candidates for contact lens usage. Unfortunately, however, they all possess the same inherent disadvantage: the molecular features required for true elastic behaviour invariably produce polymers with hydrophobic surfaces. All polymers in this group – not only the silicone-based materials – require some form of surface treatment to render them sufficiently hydrophilic for use as contact lenses, but because of the ease of chain rotation, the surfaces slowly revert to their untreated state. This problem is made worse by the virtually instantaneous elastic recovery of the materials, which causes them to ‘grab’ the cornea after being deformed by the blink. This in turn displaces the posterior tear film and leads to lens binding. Despite the attempts to harness almost every available elastomeric material, as witnessed by the patent literature, no true elastomer has been successfully used as a commercial contact lens material.
The Search for Better Materials
Once the need for a contact lens material with higher oxygen permeability than PMMA was established, a wide-ranging search began. There was, additionally, some belief that a more flexible material than PMMA would confer enhanced comfort. At first sight, the task of finding an improved material would not seem too difficult as almost all thermoplastics are less rigid and more oxygen permeable than PMMA. Several flexible thermoplastic materials have been suggested as being suitable for contact lens manufacture in the patent literature, but none of these has achieved clinical significance. The most promising results were obtained with poly (4-methylpent-l-ene), a form of which is known commercially as TPX, and with cellulose esters such as cellulose acetate butyrate (CAB). TPX and CAB resemble each other in many ways. Both polymers are less rigid and less brittle than PMMA – they can conveniently be described as ‘tougher’. The oxygen permeability of both materials is appreciably (of the order of 20 times) greater than that of PMMA ( ) and both were capable of being fabricated by moulding techniques, which are inherently cheaper than lathe cutting, this still being the most widely used method of contact lens fabrication in the 1970s. Even the fact that TPX required a surface treatment step and that both materials (especially CAB) lacked the dimensional stability of PMMA did not seem to be inhibitors to their commercial future. The fact that they became, fairly quickly, curiosity materials was largely due to the appearance, and almost instant success, of the silicone acrylates.
Hybrid Rigid Gas-Permeable Materials
The logic of silicone acrylate materials is inescapable. They combine, to a degree, the ease of preparation of PMMA and the oxygen permeability of silicone rubber. When the need to modify PMMA to improve its oxygen permeability arose, there was therefore no difficulty in recognizing that fact. The problem lays in combining such polymers to achieve a balance of properties. The origin of the problem is the fact that different types of reaction are used in the formation of the two materials. This can be illustrated by using the picture of polymers such as PMMA and hydrogels as ‘washing line’ polymers. The principle is that polymers of this type have a long backbone (i.e. the string or ‘washing line’) from which a variety of chemical groups may be suspended (the ‘washing’).
Other types of polymer, of which silicone rubber is one example, can be regarded as ‘poppet bead’ polymers. The individual units are joined just like the individual beads on a ‘poppet bead’ necklace. There is no ‘washing’ hanging from the chain and the properties of the polymer are controlled by the structure of the poppet beads themselves. The fundamental problem that prevented simple PMMA–silicone rubber combinations from being prepared is that the ‘washing line’ and ‘poppet bead’ chemistries are incompatible and beads cannot be inserted into the washing line. The requirement is that, in order to insert an individual monomer unit into an acrylate or methacrylate polymer such as PMMA, it is necessary that the monomer should have a carbon-to-carbon double bond (as shown in Fig. 11.1 ). Without the double bond the washing cannot be pegged onto the washing line. The siloxy-methacrylates that form the basis of current gas-permeable technology get round this problem in a well-recognized but nevertheless quite ingenious way. Short segments of the poppet bead chain are turned into ‘washing’ by attaching them to a chemical intermediate that contains the necessary double bond. This can be seen in the structure of the siloxy-methacrylate monomer ( Fig. 11.3 ), which in essence consists of the individual units of silicone rubber structure pasted onto a modified methyl methacrylate molecule. On the basis of this simple picture, the story of gas-permeable lenses can be unfolded.

The Gaylord Patents – Harnessing Silicon
The major advance that enabled the development of rigid contact lens materials is found in the work of Norman Gaylord at Polycon Laboratories, described in a series of patents ( ). There are two distinct aspects of this work that are worth noting. The first is the development of what has become the industry standard siloxy-methacrylate monomer, tris(trimethyl-siloxy)–methacryloxy-propylsilane ( Fig. 11.3 ), commonly referred to as TRIS. The second is the recognition of the value of incorporating fluoroalkyl methacrylates (e.g. 1,1,9-trihydroperfluoro-nonyl methacrylate; Fig. 11.4 ), principally to enhance oxygen permeability. It is important to recognize that the bonds between individual carbon atoms are not disposed at right angles to each other and that molecules are not flat but rather have three-dimensional shapes. Although this point, which has been discussed in Chapter 4 , is reflected in Fig. 11.1 , it is impractical to do so in the representation of more complicated molecules such as the siloxy- and fluoromethacrylates shown in Figs. 11.3 and 11.4 . Both these aspects of the work of Gaylord have been subsequently developed and together form the basis of most existing commercial rigid contact lens materials. Although TRIS is still the most widely used siloxy-methacrylate monomer in rigid lens manufacture, the fluoromethacrylate monomers employed in current commercial materials are much simpler than that initially used by Gaylord.

It is important to note that the concept of a fluorine-containing contact lens was not new. Fluorocarbons dissolve more oxygen than do hydrocarbons and give rise to polymers with somewhat higher oxygen permeabilities than their hydrocarbon equivalents. It was over 10 years after the first description of the advantages of contact lenses prepared from polymers derived from perfluoroalkylethyl methacrylates, in a series of DuPont patents, that significant commercial use was made of fluorocarbon-based contact lenses ( ). The reason is straightforward: there is a huge advantage in oxygen permeability of the siloxy-methacrylates over fluorocarbon methacrylates, which on their own do not produce a clinically significant balance of advantages over PMMA. The great advantage of the fluorinated methacrylates comes when they are used partially to replace methyl methacrylate in copolymers with TRIS. The balance of the three components (fluoromethacrylate, methyl methacrylate and TRIS) is adjusted to optimize oxygen permeability, hardness (which influences processability) and wettability. Although the Gaylord patents marked the beginning of the inventive thread, several other workers made significant contributions to the development of lenses with advantages in clinical practice by identifying ways of optimizing the balance of oxygen permeability, wettability and mechanical behaviour.
Within a 12-month period in 1978 and early 1979, at about the time of appearance of the third patent of Gaylord’s, three workers began to file their separate series of patents related to siloxy-methacrylate-based contact lens materials. These were, in advancing order of the priority date for the first written filing, Kyoichi Tanaka (Toyo Contact Lens), Edward Ellis (Polymer Technology) and Nick Novicky, whose later patents (and presumably rights to the earlier patent) were assigned to Syntex (United States). The Ellis and Novicky patents form a clear line of continuation from the early work of Gaylord and, because of this, are best considered together ( ). The work of Tanaka – for which parallel filings exist in Japan and the United States – has some slight and significant differences mainly concerned with the inclusion of a hydroxyl group into the siloxy monomer to improve wettability ( ). This was a significant early step in overcoming the technical obstacles to the development of silicone hydrogels, as separately discussed in Chapter 4 .
The Ellis and Salamone patents used the basic concept of Gaylord with slight but significant modifications. The more important of these uses the basic composition – described by Gaylord – based on TRIS, but claiming novelty in the additional use of methacrylic acid ( Fig. 11.5 – a hydrophilic monomer referred to but not exemplified by Gaylord) to improve surface wettability, and by the incorporation of an itaconate ester (e.g. dimethyl itaconate; Fig. 11.6 ). This composition formed the basis of the influential early range of Boston rigid lens materials.


The early Japanese patent of Tanaka marked the beginning of a rapid growth in Japanese patent activity, principally as a result of work assigned to Hoya Lens and Toyo Contact Lens. The subsequent clinical interest in the use of rigid lenses for extended wear in Japan stimulated particular interest in means of enhancing Dk . This interest was paralleled by a series of patents, which provide valuable information on the use of fluoroalkyl methacrylates in conjunction with siloxy-methacrylates, and the properties of fluoroalkyl methacrylates themselves. The properties, specifically the permeabilities of the individual homopolymers, are carefully described. It is in the Japanese patent literature, for example, that the relative permeability along the series of homopolymers of methyl methacrylate, trifluoroethyl methacrylate ( Fig. 11.7 ) and hexafluoroisopropyl methacrylate ( Fig. 11.8 ), is disclosed (1:60:100). This indicates the relative advantage, in terms of permeability, of replacing methyl methacrylate by either of these two fluoro monomers. The ground is clearly seen in this patent for the development of fluorine-containing siloxy-methacrylate gas-permeable materials (e.g. Equalens, Fluoroperm, Menicon SP), which penetrated the UK and US markets towards the mid-1980s. It is in the Japanese patents, however, that the relationship between composition and permeability of these materials is described ( ).


The readily discernible trend in the development of rigid contact lens materials described in the patent literature and discussed here is one of increasing oxygen permeability balanced against the retention of acceptable dimensional stability and ocular compatibility (characterized by wettability and deposit resistance). The essential structural developments have centred around four areas:
- 1.
The TRIS component, characterized by attempts to incorporate higher proportions of more highly branched siloxy derivatives.
- 2.
The use of fluorocarbon co-monomers in the place of hydrocarbon-based components such as methyl methacrylate.
- 3.
The improvement of wettability by incorporation of hydrophilic co-monomers, or subsequent surface modification of the formed lens.
- 4.
The development of cross-linking technology; rigid lens materials necessarily contain much higher levels of cross-linking agents than do soft lenses.
Much attention has been paid in the patent literature to the comprehensive coverage of all possible structural variants disclosed in the original patents won by Gaylord, published in 1974. Despite this, little that is truly new has appeared since then, and certainly nothing to match the leap forward brought by the identification of TRIS as a means of producing rigid contact lens materials with Dk values many times greater than PMMA. The process since that time has been one of refinement and improvement, based on the underlying principles that are contained in the patents described above.
One important refinement to increase both oxygen permeability and material strength was the introduction by Menicon of novel siloxanylstyrene monomers into the polymer backbone. Unlike its previous lenses (SFP and EX), which relied on silicone-containing methacrylate compounds for enhanced oxygen permeability, the Menicon Z material features tris (trimethylsiloxy) silyl styrene as the key monomer to fluoromethacrylate. This chemical structure results in excellent mechanical properties, allowing the lens to be significantly thinner than a typical rigid lens ( ). It was the first rigid lens material classified in the ‘hyperoxygen transmissibility’ category with a Dk of 175 and is the only rigid lens that is approved by the US Food and Drug Administration for 30 days of continuous wear. This is a variation of the styrene–HEMA polymer used in the Softperm hybrid lens. The use of styrene adds a greater resistance to flexure and a lower specific gravity.
Plasma coating has been used to good effect in silicone hydrogel materials to overcome inherent hydrophobicity. The lenses are enclosed in an ionized gas with an equal number of positively and negatively charged species. The highly charged species within the gas plasma bombard the surface of the material, and the resulting energy causes a number of changes on the surface of the material. It is used in a wide variety of applications, including highly efficient surface cleaning, or increasing hydrophilicity and even hydrophobicity. A plasma oxidation surface treatment process has been developed for the treatment of rigid contact lenses produced from the Optimum range of materials (Contamac). The manufacturers claim the processes have been optimized to produce significant improvements in the wetting characteristics, without requiring a lengthy treatment procedure.
Silicone hydrogel polymers have been very successful in the form of soft lenses but can be made with a range of water contents from 0% to 60%. At low water contents (<10%), the polymers are rigid. There are two types of rigid silicone hydrogel materials. In one type, the water content and expansion are constrained by decreasing the ratio of hydrophilic monomers and increasing the cross-link density. Thus the polymer cannot absorb water into the interior of the matrix, but the surface can hydrate like a hydrogel lens. In the second type, a reactive hydrolysable monomer is included in the formulation. This means that, when the lens is placed in water, the reactive monomer hydrolyses, producing a hydrophilic surface like a hydrogel lens. The reaction cannot proceed into the interior as expansion is constrained by cross-linking. This type also has the novel property of regenerating the hydrophilic surface if the lens surface is damaged or the lens is repolished.
Commercial Rigid Materials and Their Properties
Table 11.1 lists rigid contact lens materials that are commercially available at the time of writing. There has been some movement in recent years towards the standardization of experimental procedures for measuring material oxygen permeability (Dk). It is by no means certain, however, that all measurements quoted by manufacturers have been made to such standards. This is particularly true of the wide range of rigid lenses supplied, as they are from such a variety of sources. This fact presents a problem to the clinician in selecting materials on the basis of oxygen performance. Some cautionary comments are included here.
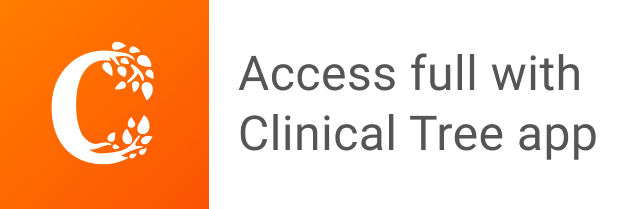