Introduction
Although lathing technology has been used to fabricate contact lenses since their invention over 130 years ago, developments over the past quarter of a century in precision engineering, materials technology and computer control systems have resulted in a capability to manufacture lenses of almost any imaginable shape – from basic spherical lens forms to highly complex aspheric designs. These developments have resulted in renewed interest in rigid lenses, and in particular scleral and corneoscleral rigid lenses, which despite representing a small minority of lenses sold are still a very important alternative form of vision correction – and indeed the only form of contact lens that will provide adequate vision in cases of corneal distortion (as occurs in keratoconus). The type of use or design of rigid lenses prescribed has shifted substantially over time. In 1996, 80% of rigid lenses were of spherical design ( ); this had dropped to 38% in 2020 ( ). The proportion of lenses requiring more specialized manufacturing techniques has risen accordingly, as is evident from worldwide rigid lens prescribing data for 2020 ( ) ( Fig. 12.1 ).

This chapter will explain the process of rigid lens manufacture and presents an analysis of the impact of regulatory constraints on the rigid lens sector. This discussion will relate primarily to the fabrication of rigid corneal lenses, although the techniques described can also be used to manufacture scleral and corneoscleral rigid lenses.
Rigid Lens Manufacture
The process of lathe cutting soft lenses has already been outlined in Chapter 5 . Here, a more comprehensive illustrative account of the process of lathe cutting will be presented in the context of rigid lens manufacture.
Raw Materials
The raw material is supplied to the lens manufacturer in the form of flat cylindrical buttons of 12.7 mm diameter and circa 4.3 mm thickness. Some types are sold with a concave depression in one surface as preparation for base curve cutting. These are supplied in various colours and the tradename of the product is typically imprinted on one surface of the button ( Fig. 12.2 ). The choice of material is largely dictated by clinical needs, with oxygen permeability being a key consideration. The latest range of rigid materials is designed as ‘super’ gas permeable with Dk values of over 150 Barrers. These materials typically require some postproduction treatment in order to ensure a wettable surface. Manufacturers often seek extended-wear approvals for lenses made from these polymers, for use in overnight orthokeratology. From the standpoint of the manufacturing laboratory, however, consideration needs to be given to the ‘machinability’ of the material, as some materials are more susceptible to surface deterioration and degradation of optical quality compared with other materials when subjected to the same manufacturing processes ( ). Manufacturing laboratories that wish to make lenses from the latest rigid materials need to use only the best types of lathes available. Typically these lathes will use hydrostatic X, Y slides and air-bearing spindles, all under sophisticated computer control.

Generating the Lens Back Surface
Some lathes are configured so that they can be used to generate both the front and back surface of the lens; however, in practice, separate lathes are used in order to optimize the lens production process. Fig. 12.3A shows a lathe configured for generating the lens back surface.

The button is first secured in a carrier, or dolly, which is a small hollow cylinder lined with plastic ( Fig. 12.3B ). This assembly is secured to a back surface lathe in a clamp, or collet ( Fig. 12.3C ) and this assembly is set spinning at a high rate about its central axis. have demonstrated that the accuracy in achieving the desired back optic zone radius can be increased by minimizing the pressure applied to the button when fixing it into the collet of the lathe.
A ‘rough’ or preparation diamond-tipped tool is automatically advanced towards the spinning button and the posterior surface lens shape is cut by advancing the diamond cutter from the edge to the centre of the button (because the button is spinning around its central axis, a cut on only one side of the button will result in the full width of the button being cut) ( Fig. 12.3D ). The waste plastic that is lathed away (swarf) is extracted via an air vacuum tube mounted above the lathe assembly. Some laboratories will strive to improve swarf and surface management by the use of suitable cutting fluids. These cutting fluids or sprays maintain a cooler surface and assist the swarf to peel away cleanly from the button surface. Any clogging of the swarf around the diamond tool will very quickly result in a pitted and overheated surface. A fine diamond tool is used to make the final surface cut so as to render a smooth, high-quality finish. With some lathes, the fine cut can be so precise as to obviate the need for polishing. This can be achieved with the use of gem-quality diamond tools, air-bearing spindles and slides and nanometre surface control. The best of these lathes can achieve a surface roughness ( R a ) close to 3–8 nm.
A diamond tool advances from the side to reduce the button diameter to the required size of the finished lens. The button is released from the lathe and the cut surface is given a brief polish – typically for about 5–30 seconds, depending on the lathe/material combination ( Fig. 12.3E ). The thickness of the button is measured at its thinnest point (centrally), and this information is programmed into the front surface lathe so that the final lens will be cut to the desired thickness.
In the process of lathing and polishing, care must be taken to avoid overheating the lens material, because the generation of excess heat can result in warpage, surface crazing ( ) ( Fig. 12.4 ) and errors in generating the desired surface curvature ( ).

Strategies employed to avoid this problem include programming the lathe to make incremental cuts rather than one continuous cutting action and passing a constant flow of air/cutting fluid over the lathing assembly to keep it cool.
Generating the Lens Front Surface
In order to generate the lens front surface, the button needs to be fixed onto a mount, or arbour (which will later be secured to a front surface lathe). This process of mounting the button onto the arbour is known as blocking. The arbour can be a metal or plastic cylindrical tool, one end of which is dome shaped so that the curve of the dome approximately matches the form of the posterior lens surface that has previously been generated. The operator heats the arbour to approximately 80°C and applies low-melting-point wax to the dome end or, in the case of a plastic tool, applies a UV-sensitive glue that can be cured to a hard form after centring. The newly cut back surface of the button is mounted onto the wax-surfaced dome of the arbour and carefully centred ( Fig. 12.5A ) via either a centrifugal means or by some form of precision alignment jig.

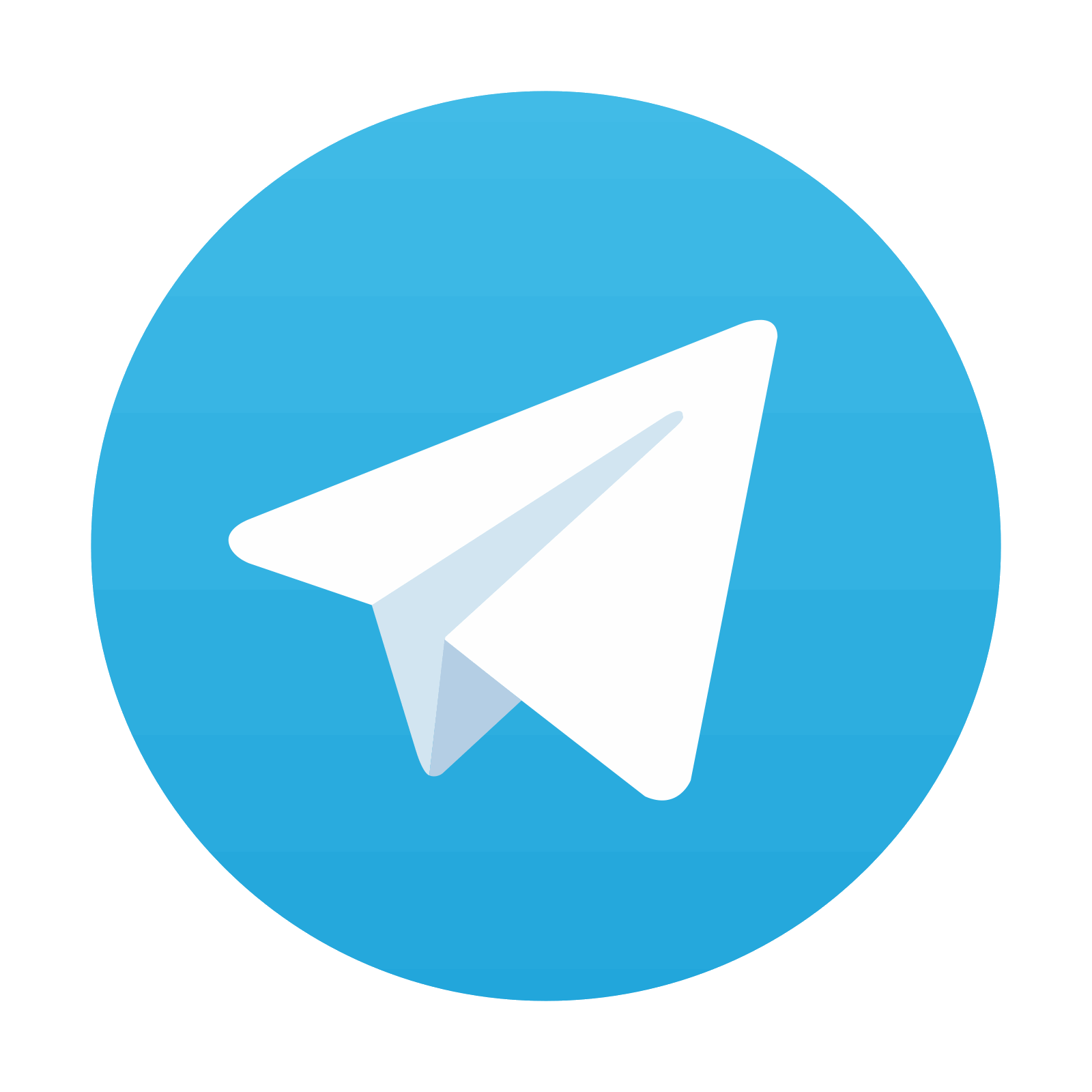
Stay updated, free articles. Join our Telegram channel
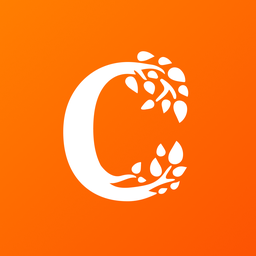
Full access? Get Clinical Tree
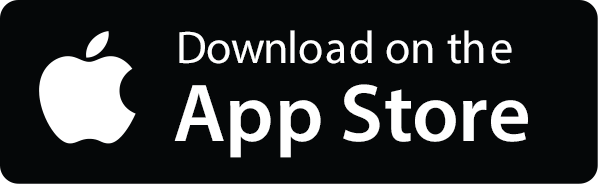

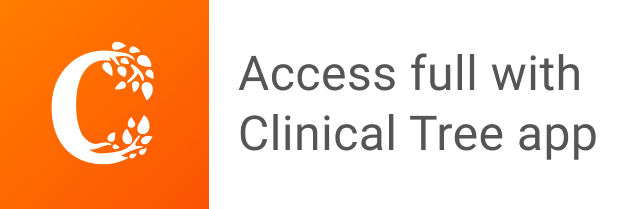