Introduction
Soft contact lenses have had a massive impact on the global contact lens market since they became widely available in the early 1970s. Since their introduction, the number of soft contact lenses being prescribed around the world has steadily increased, and it is mainly the sale of soft contact lenses that is responsible for an industry that has been estimated to reach US$10 billion globally by 2025. A recent survey has indicated that soft lenses currently make up 87% of all contact lens refits worldwide ( ).
Saturation of the contact lens market with soft lenses has occurred primarily due to two reasons. First, soft lenses provide wearers with what they see as the two most important requirements for successful contact lens wear: good vision and comfort. The major obstacle as far as rigid lenses are concerned is generally accepted as being their lack of comfort and, in particular, their initial discomfort ( ). Second, advances in manufacturing technology have directed the industry towards disposable soft lenses.
Contact lens materials (both soft and rigid) are good examples of biomaterials. A biomaterial may be defined as a natural or synthetic material that is suitable for introduction into living tissues, especially as part of a medical device. The term encompasses a vast array of technologies, including tissue engineering, artificial organs, bioceramics, medical devices and implantable drug delivery systems. Contact lenses are classified as a medical device in most countries.
Very few of us are likely to get through life without having some kind of biomaterial introduced into our bodies. The most common examples include dental fillings, contact lenses, intraocular lenses, heart valves and stents. This list in itself highlights just how diverse biomaterials must be to satisfy their very specific end application; for example, a contact lens material has very different properties compared to a material used for dental fillings.
If a biomaterial is to be successful in its application, it follows that it must also be biocompatible. Biocompatibility refers to the ability of a material to perform with an appropriate host response in a specific application. An ‘appropriate host response’ includes not having toxic or injurious effects on biological systems. Biomaterials manufactured for use as contact lenses must not only satisfy all of these requirements for safe use within the eye but must also additionally have very specific characteristics, such as being transparent (and remain so on the eye), comfortable and relatively cheap to manufacture.
This chapter reviews the building blocks, properties and characteristics of the materials that are used to manufacture soft contact lenses and provides some of the history of development of these materials. Most clinicians are familiar with the United States Adopted Name (USAN) of a particular lens material (e.g. etafilcon A or lotrafilcon A), but any further understanding of the material is often lacking. This chapter aims to give meaning and background to these USAN names to help the reader understand and differentiate between different soft lens materials.
Polymers
All contact lens materials may be classified as polymers. The word ‘polymer’ is derived from ancient Greek, meaning: ‘many parts’. Polymers are solid materials (as opposed to gases or liquids) that are made up of high-molecular-weight chains (i.e. long chains), which in turn are made up from small repeating units. These repeating units are called monomers. Polymers are macromolecules (giant molecules) made from thousands of atoms. The term ‘polymer’ is therefore an umbrella term for materials that include plastics [e.g. polymethyl methacrylate (PMMA), used in the manufacture of ‘hard’ rigid lenses]; fibres (e.g. nylon); elastomers (i.e. rubbers such as silicone rubber); and the materials being discussed in this chapter, hydrogels.
The term ‘hydrogel’ is often used interchangeably with the term ‘soft’ when referring to contact lenses. Soft lenses are so named because they are made from water-swollen, cross-linked, hydrophilic polymers that are flexible and compliant. The term ‘hydrophilic’ is used to show that the networks from which these materials are made are ‘water-loving’.
The widespread use of polymers in many areas of our everyday lives has become a common and accepted phenomenon, so much so that they have been referred to as the ‘steel of the 21st century’. Polymers possess many properties that make them suitable for a wide range of applications, some of which are unique. These properties are in part due to the length of the molecules from which they are made. Additionally, polymers derive their unique characteristics from the ability of certain atoms to join together to form stable covalent bonds.
Many polymers are composed of hydrocarbons [i.e. carbon (C) and hydrogen (H) alone] such as polyethylene and polystyrene. However, even though the basic makeup of many polymers is carbon and hydrogen, other elements can also be present. Oxygen (O), nitrogen (N), chlorine (Cl), fluorine (F) and silicon (Si) are commonly found in the molecular makeup of polymers. Many polymers have carbon backbones (these are considered organic polymers), but some can incorporate silicon or phosphorous backbones (these are considered inorganic polymers).
The atoms making up a polymer and its geometric arrangement give each polymer its chemical distinctiveness and, thus, its particular use and function. Polymers themselves may be completely natural (e.g. cellulose), partly natural (e.g. cellulose acetate) or completely synthetic (e.g. PMMA). Most of the polymers used in the manufacture of soft contact lenses fall into this last category, i.e. they are man-made.
The Structure of Polymers
A polymer chain can be described by specifying the kind of repeating units present and their spatial arrangement. In this way, several broad categories of polymer can be described.
A homopolymer is one in which only one type of monomer is used, i.e. the units are chemically and stereochemically identical, with the exception of the end units. If the chain units are arranged in a linear sequence, the polymer is referred to as a linear homopolymer. This is shown schematically in Fig. 4.1 . Departures from this simple array lead to structures of increasing geometric complexity. A nonlinear or branched structure is shown in Fig. 4.2 .


The chemical differences between linear and branched polymers may be quite small; yet, because of the structural differences, the two polymers can have quite markedly different properties. A good example of these differences is found between low-density polyethylene (branched) and high-density polyethylene (linear). Low-density polyethylene is commonly used as a packaging film (e.g. cling film and for carrier bags), whereas high-density polyethylene is used for making pipes and durable plastic bottles because of its higher impact strength.
Nonlinear and network structures can also be prepared from a collection of linear chains by covalently linking together chain units selected from different molecules. Such a system is said to be cross-linked. This is shown schematically in Fig. 4.3 . Here, X represents the chemical species (the cross-linker) that covalently links together the A units from different molecular chains. When a sufficient number of units are intermolecularly cross-linked, an infinite network is formed. A cross-linker is an important ingredient in a soft contact lens monomer mix, which will be discussed later.

A copolymer is one in which more than one type of monomer is used. The properties of a copolymer not only depend on the chemical nature and amounts of the counits but also vary markedly on how the units are distributed along the chain. For linear copolymers, three ‘ideal’ arrangements can be described. The first is an alternating copolymer, which is shown in Fig. 4.4 . In this scenario, each monomer prefers to interact with a fellow monomer rather than itself.

At the opposite extreme is the ordered or block copolymer, where there is an overwhelming tendency for a unit to be succeeded by another of the same kind. Here, long sequences of one type of unit alternate with long sequences of another kind ( Fig. 4.5 ).

The third major classification is the random copolymer. Here, different units are randomly distributed along the chain ( Fig. 4.6 ).

Departing from the restrictions of a linear array, branched copolymers, known as ‘graft polymers’, can also be prepared. The backbone of the molecule is composed of one type of unit, and the long side chains, or grafts, are made up of another. More sophisticated types of graft polymers have backbones made up of different repeating units and several distinctly chemically different side groups. This type of polymer is represented schematically in Fig. 4.7 .

One final important classification of polymers is into either amorphous or crystalline polymers (i.e. their macromolecular order) ( Fig. 4.8 ). Crystalline polymers have a geometrically regular structure and are generally stiff, resistant to chemicals, and tough. They have limited use as materials for contact lenses owing mainly to their poor optical qualities (i.e. they tend to be translucent or opaque). A good example of a semicrystalline polymer is polypropylene, which is often used to make casts in the cast-moulded manufacturing process of contact lenses.

Amorphous polymers, on the other hand, do not have a regular structure. The polymer chains intermingle and are in random positions (imagine a pile of spaghetti on a plate), which often allow for these polymers to be transparent. Depending on their chain mobility, amorphous polymers can be classified as either ‘plastic’ or ‘glassy’ ( ).
Polymerization
The chemical reaction that monomers undergo to form long-chained polymers is known as polymerization. Broadly speaking, monomers can be chemically joined together in two ways: by step growth (condensation) and chain growth (addition) processes. Condensation polymers are produced by the reaction of monomeric units with each other, resulting in the elimination of a small molecule (e.g. water). However, hydrogels are generally formed through chain growth (addition) polymerization.
Before entering into the intricacies of polymerization, it is important to establish that to make a contact lens material, the following three basic ‘ingredients’ are required in the monomer ‘mix’: (1) the monomer(s), (2) a cross-linking agent and (3) an initiator. In some cases, a solvent is also added to the monomer mix. A solvent is used when lenses are manufactured by ‘wet casting’, where the solvent is gradually replaced with saline. If a solvent is not used, the manufacturing process is often referred to as ‘dry casting’ (i.e. the contact lens is cast as a xerogel).
The monomers used in chain polymerization are unsaturated and sometimes referred to as vinyl monomers. Essentially, this means that the monomer has one or more carbon-to-carbon double bonds. During the polymerization process, the monomer concentration decreases steadily with time, resulting in a reaction mixture that contains monomer, high-molar-mass polymer, and a low concentration of growing chains. Chain polymerization is characterized by three distinct stages: initiation, propagation, and termination.
Initiation
A hydrogel monomer mixture usually contains an initiator. This is a chemical whose role is to start the polymerization process. Initiators readily fragment into free radicals (a highly chemically reactive atom, molecule or molecular fragment with a free or unpaired electron) when activated by heat or some other form of radiation (e.g. ultraviolet light).
The type of initiator used depends on the manufacturing method. For example, a thermal initiator is usually required in the manufacture of buttons or rods that eventually form lathed lenses, and a photoinitiator is usually required for spun-cast and cast-moulded lenses.
The fragmentation of the initiator is schematically represented by the following equation, where I represents the initiator molecule and I • represents a free radical.
I−IΔ→2I•
The free radicals formed are then able to combine with the monomer (M), resulting in a free radical of the monomer (this is why the polymerization of hydrogels is sometimes referred to as free radical polymerization).
<SPAN role=presentation tabIndex=0 id=MathJax-Element-2-Frame class=MathJax style="POSITION: relative" data-mathml='I•+M→IM•’>𝐼•+𝑀→𝐼𝑀•I•+M→IM•
I • + M → I M •
Propagation
The monomer radical, which is a transient compound, is now able to combine with another monomer unit, resulting in another new compound
IM•+M→IMM•
By the continuation of this process, the polymer chain is propagated. The resultant chain may consist of thousands of monomer units
IMn•+M→IM(n+1)•
Termination
Polymerization does not usually continue until all of the monomer has been used up because the free radicals involved are so reactive that they inevitably find a variety of ways of losing their reactivity. Polymerization can be terminated in two main ways. The first method is recombination. This occurs when two growing molecules containing free radicals meet, share their unpaired electrons and form a stable covalent bond, thereby extinguishing their reactivity. The second method of termination is known as disproportionation. This occurs when two radicals interact via hydrogen abstraction, leading to the formation of two reaction products, one of which is saturated and the other unsaturated.
The conditions under which polymerization takes place become important when one considers that soft contact lenses can be made using three main methods of manufacture: lathing, spin casting and cast moulding; however, cast moulding is by far the most commonly used method. Lenses made by these different methods of manufacture undergo very different polymerization conditions that are likely to have an effect on the resultant material. How a material is processed is likely to affect almost every aspect of a lens, from its clinical performance to its physical and chemical properties ( ).
Hydrogel Materials
Soft lens materials can be conveniently divided into two main groups: (1) hydrogel materials (now sometimes referred to as low- Dk materials) and (2) silicone hydrogel materials (high- Dk materials). This section describes hydrogel materials.
Hydrogel lenses were developed as a result of the extraordinary pioneering efforts of Professor Otto Wichterle and Dr Drahoslav Lim of the Institute of Macromolecular Chemistry of the Czechoslovak Academy of Sciences in Prague in the mid-1950s. Wichterle and Lim were working on the synthesis of a new material that they hoped could be used for implantation into the human body. That material was poly(hydroxyethyl methacrylate) or pHEMA ( ). They soon realized that the material had potential applications in the manufacture of contact lenses but were prevented from researching such a project by the directors of the institute, who perceived this work as being a petty distraction from fundamental studies in chemistry. Wichterle was eventually forced to carry out his contact lens experiments at home and, despite such difficult circumstances, he successfully managed to produce the first spun-cast lens (made from his son’s toy construction set) in 1961 ( ). The enormity of his breakthrough for the contact lens industry cannot be understated.
pHEMA is made by polymerizing 2-HEMA monomer with a cross-linker such as ethylene glycol dimethacrylate ( Fig. 4.9 ). Most of the hydrophilic behaviour of HEMA is due to the presence of the hydroxyl group (OH) at the end of the monomer. At this location, hydrogen bonding with water molecules occurs, causing them to be drawn into the polymer matrix. The result is that contact lenses made from pHEMA contain approximately 40% water in the fully hydrated state.

Lenses fabricated from pHEMA were first distributed in western Europe in 1962, but the sales were disappointing. In 1965, the National Patent Development Corporation bought the licence for the American rights to the technology from the Czechs. This was subsequently sold on to Bausch & Lomb, which at that time manufactured ophthalmic equipment and spectacle lenses. Bausch & Lomb significantly refined Wichterle’s spin-casting process and finally obtained approval from the US Food and Drug Administration (FDA) for its pHEMA lenses in 1971. This time, the lenses became very popular very quickly; both practitioners and patients enjoyed the benefits of increased comfort, reduced adaptation time, and easier fitting procedures compared with rigid corneal lenses, which were the main alternative. With time, more companies developed their own pHEMA lenses; however, it soon became clear that these lenses were not problem-free. Corneal hypoxia was the main problem, but other complications relating to solution toxicity and lens spoliation were also common.
In hydrogel materials, oxygen is transported through the water channels in the lens and not the polymer itself. Contact lens manufacturers, therefore, had two possible avenues to follow to increase the oxygen transmissibility of lenses: develop ‘hyperthin’ lenses or develop materials with higher water contents. Producing lenses that were thinner was a relatively straightforward matter for lens designers, and several of these lenses were launched, such as the Hydrocurve thin lens (Soft Lenses) in 1977 and subsequently the O3 series (Bausch & Lomb). These lenses were in the range of 0.035–0.06 mm thickness, which was less than half the thickness of the original Bausch & Lomb pHEMA lenses.
Developing materials with a higher equilibrium water content (EWC) led to the successful development of HEMA copolymers. One of the first successful copolymerizations was with N -vinyl pyrrolidone (NVP) (see Fig. 4.9 ). The amide (N–C=O) moiety is very polar, and two molecules of water can hydrogen-bond to it. NVP-based copolymers lose the slippery feel of pHEMA and consequently can be felt as being quite rubbery. These copolymers also tend to have relatively high evaporation rates of water, which may be seen as a problem for lens stability and comfort. This occurs because the amide group does not bind water as strongly as a hydroxyl group. In addition, these polymers are also significantly more temperature-sensitive than pHEMA-based materials; that is, their parameters tend to change with increasing or decreasing temperature. This is important when fitting a lens as its parameters may change on the eye.
NVP-based lenses have also been associated with increased corneal staining (solution-induced corneal staining or ‘SICS’) and decreased comfort when used in conjunction with solutions containing higher levels of polyhexanide ( ). This does not mean that polyhexanide-based solutions cannot be used with NVP-containing lenses, but rather that the interaction should be borne in mind, and if any significant corneal-staining or discomfort symptoms arise, these can usually be treated simply by changing the solution to one containing a lower level of polyhexanide or one free from polyhexanide. More recent research however has indicated that it may be the surfactant in the solution that may cause this transient corneal staining ( ).
Most contact lens practitioners are familiar with methyl methacrylate (MMA) as the hydrophobic material from which ‘hard lenses’ are made (i.e. PMMA) (see Fig. 4.9 ). When MMA and NVP are copolymerized, a completely new material is obtained with very different characteristics from those of HEMA/NVP (also known as HEMA/VP copolymers). Depending on their composition, contact lenses made from MMA/VP copolymers can contain 60%–85% water. MMA is very hydrophobic but is useful in soft lens hydrogels as it gives the resultant polymers increased mechanical strength.
Another hydrophilic monomer that has been very successfully used in contact lens hydrogels is methacrylic acid (MAA) (see Fig. 4.9 ). When added to a soft lens polymer formulation, it results in a soft lens with ionized groups (negatively charged) within the polymer matrix, allowing for the lens to absorb more water. The higher the amount of MAA, the higher the EWC of the resulting polymer. Amounts of MAA in the range of 1.5%–2.5% increase the water content of a HEMA material into the mid-water-content range of 50%–60%, thereby allowing for oxygen permeability to increase significantly. Another advantage of these ionic lenses is that although they attract large quantities of protein (particularly, positively charged lysozyme) ( ), a large proportion of these proteins is in the natural, nondenatured form ( ), which is thought to be beneficial for the health of epithelial cells ( ), and reduces contact-lens-related complications such as contact lens papillary conjunctivitis. There may also be a link with improved comfort ( ). Additionally, proteins in their active state (as opposed to being denatured) have increased antimicrobial activity ( ).
Unfortunately, using MAA to increase the water content of a polymer also has its disadvantages. These include
- •
A lens that is extremely sensitive to changes in tonicity ( ): the Na + ions present in saline solution have the effect of ‘shielding’ the carboxylate anions. In hypotonic solutions (e.g. pure water), since these shielding ions are present to a far lesser degree, more chain repulsion occurs, which increases the swelling of the network and consequently the EWC of the material. In hypertonic solutions, the reverse situation occurs and the material network shrinks, causing its EWC to decrease.
- •
A pH-sensitive lens ( ): if the pH of the solution in which the lens is immersed is decreased (i.e. the hydrogen ion concentration is increased), the carboxylate anions are more shielded and the network becomes less expanded. This causes a decrease in the lens EWC.
- •
Dimensional instability when the lens is heat-disinfected.
Glyceryl methacrylate (GMA) is more hydrophilic than HEMA owing to the fact that the monomer contains two hydroxyl groups (see Fig. 4.9 ). This monomer has been used in contact lens materials in two main ways. The first method uses GMA in combination with MMA to produce materials that have water contents in the range of 30%–42%. These materials are thought to be stiffer and stronger than pHEMA hydrogels, but their oxygen permeabilities are not ideal for in-eye use.
The second method uses GMA in combination with HEMA to produce high-water nonionic contact lens materials (up to approximately 70% has been possible). These contact lenses are said to be ‘biomimetic’, that is, it is claimed that they improve biocompatibility by imitating the hydrophilic properties of mucin. Manufacturers also suggest that these lenses show a low rate of dehydration and a rapid rate of rehydration (i.e. they have good ‘water balance ratios’). In addition, the materials are thought to be relatively deposit-resistant and seem to be insensitive to pH changes in the range of pH 6–10. An example of such a lens is the hioxifilcon A material used in the Clear 1-Day lenses manufactured by Clearlab. Another example of the so-called biomimetic lens is the Proclear lens (Coopervision), which contains phosphorylcholine (PC) and HEMA. PC is said to mimic the natural chemistry of cell membranes.
In the early 1970s, an English optometrist, John de Carle, proposed that if the EWC of hydrogel lenses could be sufficiently increased, then these lenses could be worn successfully on an overnight or extended-wear basis. He developed the first extended-wear lens to be distributed in the United Kingdom, known as Permalens ( ). The lens material had an EWC of 71% and was made from a HEMA/VP/MAA copolymer. In 1981, the lens was given FDA approval for ‘extended wear’ of up to 30 days along with another lens, the Hydrocurve II (Wesley Jessen).
Slowly, other lenses were given approval for extended wear during the 1980s, but along with the increase in demand for these lenses came an increase in complications. In 1989, studies were published showing that the risk of microbial keratitis was 5–15 times greater for extended wear than for daily wear ( ). As a result, the FDA recommended that extended wear be limited to six consecutive nights, and, with that, the enthusiasm for extended wear died down to some extent until the emergence of silicone hydrogel lenses in the late 1990s.
Table 4.1 lists some of the most common hydrogel lenses on the market and groups them into their appropriate ISO classification (see Appendix 4.1 at the end of this chapter for details on the classification of hydrogels).
Name | Manufacturer/Supplier | Principal Components | EWC (%) | USAN Nomenclature |
---|---|---|---|---|
ISO Group 1 (<50% EWC, nonionic) | ||||
SofLens 38 | Bausch+Lomb | HEMA | 38 | Polymacon |
Durawave | UltraVision CLPL | HEMA, GMA | 49 | Hioxifilcon B |
Hydrofit 38 | Cantor & Nissel | HEMA | 38 | Polymacon 1 |
Quattro | mark’ennovy | HEMA, GMA | 49 | Hioxifilcon B |
ISO Group 2 (>50% EWC, nonionic) | ||||
Biotrue One day | Bausch+Lomb | HEMA, VP | 78 | Nesofilcon A |
Dailies AquaComfort Plus | Alcon | PVA | 69 | Nefilcon A |
Omniflex | CooperVision | MMA, VP | 70 | Lidofilcon-A |
Proclear | CooperVision | HEMA, PC | 62 | Omafilcon B |
SofLens daily disposable | Bausch & Lomb | HEMA, VP | 59 | Hilafilcon B |
UltraWave | UltraVision CLPL | HEMA, GMA | 57 | Hioxifilcon A |
ISO Group 3 (<50% EWC, ionic) | ||||
Accusoft a | Ophthalmos | HEMA, PVP, MAA | 47 | Droxifilcon-A |
Comfort Flex a | Capital Contact Lens | HEMA, BMA, MAA | 43 | Deltafilcon-A |
Soft Mate II a | CIBA Vision | HEMA, DAA, MAA | 45 | Bufilcon-A |
ISO Group 4 (>50% EWC, ionic) | ||||
1-Day Acuvue Moist | Johnson & Johnson | HEMA, MAA | 58 | Etafilcon A |
Biomedics 55UV Evolution | CooperVision | HEMA, MAA | 55 | Ocufilcon D |
Freshlook Colors | Alcon | HEMA, MAA | 55 | Phemfilcon A |
Permalens a | CIBA Vision | HEMA, VP, MAA | 71 | Perfilcon-A |
Most of the work that has been carried out on ‘improving’ hydrogel lenses has been channelled towards developing them into disposable lenses and especially into daily disposable lenses. To achieve this, manufacturers have invested in more sophisticated automated manufacturing technologies to meet demand and make their production economically viable. This has been no easy task, and it should be emphasized just how important these hydrogel materials still are to the contact lens industry today.
Additionally, ‘enhanced’ daily disposable lenses replaced previous versions of the lenses such as 1-Day Acuvue Moist (Johnson & Johnson), Dailies AquaComfort Plus (Alcon) and SofLens (Bausch & Lomb) daily disposable lenses. These lenses utilize techniques of macromolecular entrapment and/or release of hydrophilic surface-active polymers at the lens surface to improve the end-of-day comfort by stabilizing the prelens tear film.
The Dailies AquaComfort Plus lens is manufactured from nelfilcon A, which consists of a cross-linked functionalized polyvinyl alcohol (PVA) macromer with the addition of nonfunctionalized PVA ( ). This unfunctionalized PVA macromer is free to elute from the lens into the tear film with each blink. This PVA is thought to emerge from the lens matrix as ‘strands’ at the lens surface, and it is this effect together with the effect of soluble PVA in the tear film that is referred to as the ‘surface modification’ of these lenses. The released PVA may improve lens comfort by decreasing the surface tension of the tears or by mimicking mucin, found naturally in the tear film ( ). The blister packaging also contains hydroxypropyl methylcellulose, which is a lubricating agent used to improve comfort on lens applications, and polyethylene glycol, which is a hydrophilic wetting agent with high affinity for PVA used for enhancing comfort throughout the day.
PVA and polyvinyl pyrrolidone (PVP) are common soluble polymeric components in comfort drops and artificial tears and have a viscous consistency at elevated concentrations and molecular weights, giving them good surface spreading characteristics. The 1-Day Acuvue Moist lens is manufactured from the etafilcon A polymer (HEMA/MAA) together with the incorporation of small concentrations of low-molecular-weight PVP into the ionic material network. Here, the PVP is ‘locked’ into the lens matrix and is not released from the lens during wear. The PVP is adsorbed on to the preformed lens surface after manufacture from solution. The lens packaging states that the lenses are supplied in ‘buffered saline with povidone’. Povidone is another name for PVP. PVP is quite polar, and it is likely to be relatively strongly attracted to the etafilcon material, potentially providing a mechanism for its retention on the lens surface. The persistence of PVP at the lens surface during wear has been verified by , who have also described PVP as being in a predominantly ‘looped structure’ across the lens surface. PVP is thought to reduce the coefficient of friction (CoF) of the lens surface.
The SofLens daily disposable lens is modified by the adsorption of Tetronic 1107 – a hydrophilic surface-active polymer composed of ethylene oxide/propylene oxide block copolymer – onto the lens surface. The Tetronic at the surface lowers the CoF of the lens, but it has been shown to be progressively lost from the surface during wear ( ). It is likely, therefore, that the Tetronic is held by weak forces at the lens surface, which explains the lowest in-eye persistence of three ‘enhanced’ lenses investigated by Ross et al. in 2007.
The ocular environment places significant demands on the performance of hydrogels as biomaterials. These materials must
- •
maintain a stable, continuous tear film;
- •
be permeable to oxygen to maintain normal corneal metabolism;
- •
be permeable to ions to maintain on-eye movement;
- •
be comfortable;
- •
provide clear, stable vision; and
- •
be durable for the lifetime of the lens.
These essential properties are expanded upon below.
Optical Transparency
A hydrogel to be used as a contact lens material needs to be transparent to achieve maximal visual performance. The light transmittance of polymers includes the description of materials as being transparent, translucent, or opaque. Transparent polymers are those that you can see through, translucent polymers are those that you cannot see through but allow for light to pass through, and opaque polymers are those that you can neither see through nor allow for light to pass through. Usually, the optical clarity of contact lens materials is expressed as the percentage of transmission of the visible electromagnetic spectrum. Hydrogels that are useful as contact lens materials transmit over 90% of light in the visible part of the spectrum.
When a hydrogel loses its transparency, it is likely to be due to microphase separation of water. This is due to regions of differing refractive index being formed within the gel. Hydrogels that show this type of behaviour (typically synthesized by making copolymers with large blocks or segments of hydrophobic and hydrophilic monomers rather than randomly dispersing them) do have advantages in terms of enhanced strength and permeability performance.
If the phase separation is limited (e.g. the phase size is shorter than the wavelength of light), transparent materials can still be obtained. Some hydrogels are known to lose their transparency when heated, and this is an important consideration as there is an increase in temperature from lens packaging to eye and, although rare, some patients still thermally disinfect their lenses.
Trying to combine hydrophilic hydrogel monomers and hydrophobic silicone-based monomers into transparent hydrogels was a major technical difficulty during the development of silicone hydrogel materials. likens this technical challenge to trying to mix oil with water.
Mechanical Properties
The mechanical properties of hydrogel contact lenses are fundamentally important because they are directly related to factors such as comfort, visual performance, fitting characteristics, physiological impact, durability and handleability of the lenses.
In the hydrated state, most hydrogels are soft and flexible. When they are allowed to dehydrate, they become hard and brittle. Lower-water-content polymers tend to become harder and more brittle than higher-water-content materials. Hydrogels take up water because they are hydrophilic; that is, hydrogels swell in water (as well as many other liquids), which causes them to become soft with elastic properties (the water acts as a plasticizer).
Unlike perfectly elastic materials, which deform under stress but return to their original size and shape when the stress is released, hydrogels are viscoelastic. This means that they deform time-dependently when a stress is applied to them and recover time-dependently when the stress is removed. Theoretically, this can result in permanent deformation of the material.
One of the main difficulties in characterizing the mechanical properties of a contact lens is that there is no single property measurement that accurately reflects its ‘in-use’ situation. Traditional material mechanical testing involves applying a deforming force (the ‘stress’) to a sample and observing the way that the sample responds (the ‘strain’).
Stress can be compression, tensile or shear. Compression is a stress that acts to shorten an object. Tension is a stress that acts to lengthen an object. Shear is a stress that acts parallel to a surface. Strain is defined as the amount of deformation an object undergoes compared with its original size and shape. When a tensile stress is applied to a material, the stress gradually builds up until the specimen breaks (fractures).
A generalized stress–strain curve is shown in Fig. 4.10 , and it provides several mechanical characteristics of the material under test. The strength of a material is defined as the force per cross-sectional unit area required to cause failure when the sample is subjected to a particular type of stress. Some materials go through a yield point, which is defined as the stress at which a material begins to deform plastically. Contact lens hydrogels typically do not demonstrate a yield point. Young’s modulus ( E ), or the elastic modulus, is determined by the initial slope of the stress–strain curve and is, therefore, a constant (i.e. it is the stress divided by the strain). Young’s modulus and the thickness of the material ( t ) are related in determining the stiffness of a lens. Just as Dk/t indicates the relative transmissibility of different lenses, so the stiffness factor multiplied by the thickness ( E × t ) indicates the relative resistance to deformation of the lens.
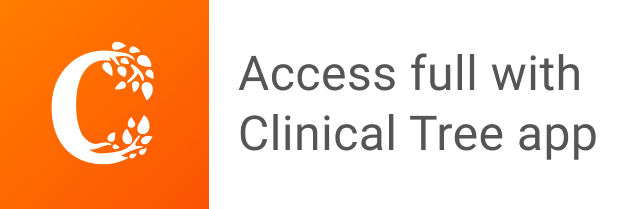