Introduction
Three techniques are currently employed to manufacture soft contact lenses – lathe cutting, spin casting and cast moulding. A fourth disruptive technology, three-dimensional (3-D) printing, has also been proposed, but 3-D-printed soft contact lenses have yet to be produced commercially.
As medical devices that rest against the highly sensitive eyeball, contact lenses need to be of the highest quality in terms of their physical construction. As devices that correct optical defocus, the optical quality of contact lenses must also be of the highest order. At the same time, it must be recognized that companies will manufacture contact lenses only if they are profitable; the dominant forces in the market dictate that these high-quality products must be delivered at minimal cost, and one consequence of this is a simplification of lens parameters to streamline the high-volume process.
Methods of Manufacture
A key requisite of any technology employed to manufacture a medical appliance is that the final product is safe, predictable and of high quality so that it meets the intended need. The three technologies discussed below have been developed to meet these requirements.
Lathe Cutting
This process essentially involves the use of a special contact lens lathe to cut an anhydrous cylindrical button of material (xerogel) into the required shape and then to hydrate this to form the finished soft lens. Lathe manufacture ranges from labour-intensive, manual-based cutting systems to sophisticated and fully automated manufacturing lines, depending on the capital budget or skill levels available ( Fig. 5.1 ). Even with the use of automation, however, the number and variability of manufacturing steps that are necessary for lathe cutting mean that manufacturing soft lenses using this technology is necessarily more expensive than using spin casting or cast moulding.

Therefore lathe cutting is generally reserved for the production of custom-ordered or extreme-range lenses that contain design features not amenable to mass production, such as lenses of high spherical power and/or high toric power, or aberration-correcting soft lenses for keratoconus ( ).
The raw xerogel is supplied to the lens manufacturer in the form of ‘rods’ or ‘buttons’. A rod is a solid cylindrical piece of xerogel, about 16 mm in diameter and 400 mm in long. The rod is then sliced, orthogonally to the long axis, into buttons about 10-mm thick. More commonly, the xerogels are fabricated and supplied in button form. When this occurs, buttons have usually been pretrimmed to an industry-standard size so that they can be machined in most of the available lathes.
The button is first secured to a back surface lathe in a clamp or ‘collet’, and this assembly is set spinning at a high rate (typically 8000–12,000 rpm) about its central axis. A diamond-tipped tool cuts the posterior surface lens shape into the button. A second diamond tool advances from the side to reduce the diameter to the required size. The surface is rendered smooth by either fine machining or polishing. Modern sophisticated lathes are capable of cutting xerogel surfaces to a tolerance of 8–15 nm. Such smooth surface finishing precludes the need for polishing and is preferred when nonspherical surface geometries are being generated. This approach also serves to preserve the consistency of one surface to the next. The dimensions of the lathed surface are calculated to allow for eventual expansion when the xerogel is later hydrated.
The button is removed from the collet and the cut posterior surface of the button is mounted onto a support tool of a front surface lathe, using low-melting-point wax. It is essential during this process that the button is mounted and fixed in an absolutely concentric and level aspect to the support tool in order to minimize unwanted prism being introduced by the front surface cutting. A diamond-tipped tool cuts the anterior surface down to the required thickness, and the surface is smoothed. The most advanced lathes offer ‘W’ axis cutting options that can generate rotationally nonsymmetric surfaces whilst the primary front surface is being cut. Polishing tools may be used to smooth the lens edge, although some advanced lathes obviate this step.
After inspecting and measuring all relevant dry lens parameters, the lens is hydrated in normal, unpreserved saline until it is fully equilibrated and impurities have been extracted. The hydrated lens is re-inspected for final wet parameter conformity, sealed in small glass vials and autoclaved at 120°C for at least 15–20 minutes to effect sterilization. Advances in lathing technology and computer-controlled processing have led to the development of semiautomatic systems whereby stacks of buttons are automatically fed into lathes; however, even this technology cannot match the mass-production capabilities of cast moulding.
Fig. 5.2 is a schematic flow diagram illustrating the process of manufacturing a soft contact lens using lathe-cutting technology.

The process of manufacturing rigid contact lenses by lathe cutting is very similar to the process described above – the key difference being that, with soft lens manufacture, the xerogel must eventually be hydrated and sterilized, whereas rigid lenses need only to be cut to their final shape and polished. Other notable manufacturing differences concerning materials of high gas permeability are tighter manufacturing tolerances and the requisite for more critical control of cutting and mounting temperatures in order to preserve their in vivo wetting properties. A pictorial account of this process of rigid contact lens manufacture, and an explanation of how toric lenses are made using lathe cutting, is given in Chapter 12 .
Spin Casting
In this process, a convex ‘male-shaped’ stainless steel tool, or ‘insert’, is produced on a high-precision engineering lathe and lapped to provide an accurate surface that matches the dry dimensions of the proposed anterior surface of the contact lens. Modern nonferrous materials are also suitable for producing the mould tool and these materials can be generated on ‘nano-accurate’ single point turning lathes. These lathes can cut mould tools to a surface finish that renders polishing unnecessary. The final surface shape of the master mould tool is verified using interferometry or other similar noncontact measuring methods. Any given tool is used to make hundreds of thousands of moulds.
The metal tool is impressed against heated liquid polypropylene or polyvinyl chloride, which then cools and sets to form a solid plastic concave female mould. Numerous metal tools (typically 8×–12×) are used to produce the same number of plastic moulds simultaneously. The moulding methods and tooling used must be very accurate in order to preserve the concentricity of the resultant plastic part. Any moulding runout will create an unwanted prism in the lens during the spinning process. This type of injection cast moulding is generally conducted in a controlled environment (usually to a class 100-K level). It is imperative for a spin-cast manufacturing process to control the level of potential contaminants to a minimum as it is an open-moulding system.
The xerogel lens form is created by pouring liquid monomers into the concave moulds, which spin at a controlled rate about the central mould axis.
This spinning takes place in a controlled atmosphere of nitrogen or a similar oxygen-deprived atmosphere ( Fig. 5.3 ). This is necessary as the spin mould is an open system and thus exposes one surface of the lens (posterior) to air as it is being cured. Oxygen in the air is a natural scavenger of the initiator and will ultimately inhibit the polymerization process.

The speed of rotation, combined with both the mould tool shape and monomer dose, ultimately determines the final lens parameters. The shape of the back surface is primarily governed by the centrifugal force generated by the rate of spin of the mould, surface tension forces between the mould and polymer and the effects of gravity. A greater speed of rotation of the mould will result in more polymer mass being shifted towards the lens periphery and more negative lens power. Due to this system of manufacture, certain process controls such as monomer dosing must be more accurate than those found in full cast moulding of contact lenses.
As the mould spin rate stabilizes, ultraviolet radiation and/or heat is introduced to initiate polymerization. The lens is removed from the mould, and the mould is discarded. Certain spinning processes hydrate the lens in the original plastic mould and it is never removed. This process has proven advantageous and cost-effective for the mass production of daily disposable lenses.
Other spinning systems still require that the edges of the lens are polished and that the lens be inspected, hydrated, re-inspected, packaged and autoclaved. Spin casting can produce a much higher output volume than lathe cutting and in the latest systems can match the high volume of lenses that can be produced by cast moulding. The primary restriction of spin-cast manufacture lies in its inability to generate a fully formed edge from the posterior to anterior surface; however, sophisticated design modelling, combined with accurate tooling, has largely mitigated this limitation. The process of spin casting is illustrated in Fig. 5.4 .

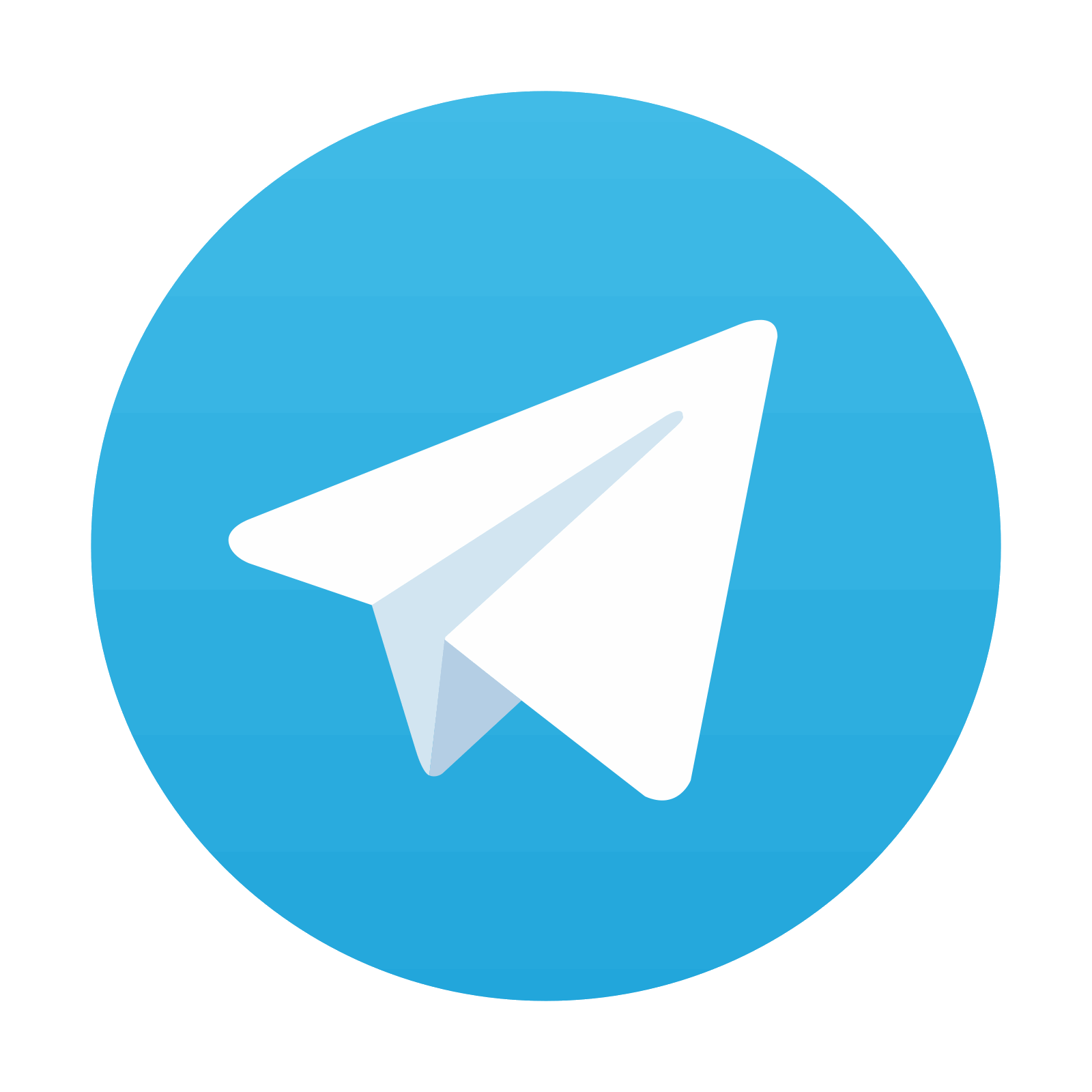
Stay updated, free articles. Join our Telegram channel
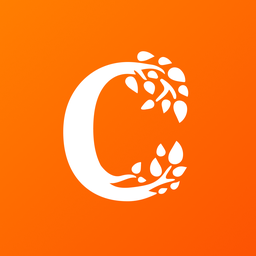
Full access? Get Clinical Tree
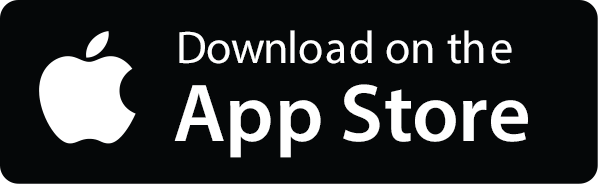

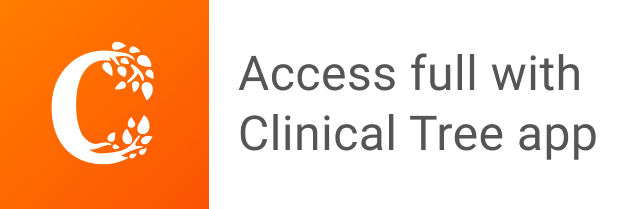