Introduction
The clinical success of crosslinking was made possible by the development of ultraviolet (UV)-light emitting diodes (LEDs) that allowed for a reasonable balance of cost and performance with reliable control and dependable performance, which are essential for the scientifically verifiable results. Crosslinking technology has experienced fast growth and improvement since its introduction in the beginning of the 21st century, mainly owing to the development of low-cost, highly efficient and reliable UV-light sources.
Crosslinking Equipment: Common Architecture and Internal Parts
It is important to understand that the internal architecture of the crosslinking platforms must present similar components and system-level internal blocks, mainly due to safety regulations, as will be discussed later.
Crosslinking equipment based on the current technology consists of the following main parts:
- •
UV source and its electronic control system
- •
Optical beam delivery system
- •
Main system electronics and human interface
UV-Light Source
There are several UV-light sources, such as xenon discharge lamps, deuterium lamps, fluorescent mercury arc lamps, and high-temperature halogen lamps. Although these technologies can deliver considerable amounts of UV light, the light spectrum emitted is broad, and the spectral power density is very low in the UV region of interest for riboflavin-based crosslinking.
Initially, very-narrow-band interference light filters had been employed to allow only the UV region of interest to be delivered onto the corneal tissue. Therefore very-high-power sources and high-power electronics were needed at that time. The development of moderate-power LEDs in the UV spectral region changed this scenario in the beginning of the 21st century. Light emitting diodes had been established since the semiconductor revolution at the beginning of the 1960s. Initially, only infrared, red, and green emitting diodes were feasible, with progressively higher output power and broader visible spectral coverage. In the late1990s, consequent to new dopants and semiconductor structures, the development of LEDs composed of indium gallium nitride semiconductors allowed emission in the UVA spectrum (315–400 nm). An interesting history of the development and principles of operation of such blue and UV devices can be found elsewhere.
Briefly put, an LED emits photons in a predetermined spectral region owing its material constituents and the existence of enough density of charge carriers, electrons, by means of carefully controlled voltage and current applied. Medical use of LEDs is based on specific behavior and performance characteristics. Some of the most important subjects in this field will be discussed.
Wavelength Selection
Owing to its internal tolerances and material variations, a typical UV LED does not present a precisely tuned wavelength and viable devices must be selected in each production batch. For instance, a typical 365-nm device production batch shows around ±10 nm peak position distribution. Therefore when selecting the device, it is necessary to specify the tolerance of the desired wavelength. Factory standard selection classifies devices on ±3 nm peak position range bands. This tolerance centered on 365 nm is well inside the riboflavin/tissue crosslinking reaction confidence area.
Temperature Influence on Wavelength
As with any semiconductor, the peak wavelength varies with temperature. Typical variation values are about 0.02 nm/C° in LED UV devices, which is considered a very stable emission. Under the recommended operational range of temperature for clinical use and the assistance of a closed-loop power control, there is very low risk of wavelength slippage that could compromise its performance. Aging also influences semiconductor devices, and some wavelength deviation is possible, but all LED UV devices present on the market remain inside ± 2 nm through their entire lifetime.
Temperature Influence on Power Output
Power output is strongly dependent on semiconductor temperature. The performance of the LED decreases with increasing temperature. This dependency makes it impossible to control the device’s UV emission based only on a constant voltage or current. A closed-loop control must continuously sample the UV output power and modulate the current applied to reach the desired value at a certain time.
The UV Light Optical Beam Delivery System
Key factors of crosslinking equipment are optical beam output shaping and control.
Optical Output Power Density Distribution
Many of the UV LED sources employed in crosslinking procedures are selected owing to their power output requirements. Unfortunately, in the required power range, all devices are composed of a group or an array of very small emitters tied together, assembled and electrically connected on the same thermal substrate. Consequently, the light-emitting surface is not homogeneous and shows very strong power variation and power density fluctuation. This characteristic imposes a critical constraint as the riboflavin/tissue interaction is highly dependent on power density. Therefore the optical system must employ techniques to create a virtual source with a homogeneous profile. Otherwise, a heterogeneous power distribution on the corneal surface may cause differential deformation, called hot spots . Hot spots may cause nonuniform results and localized endothelium cell damage and haze, especially in thin corneas.
Fortunately, there are several optical design methods that can be employed that are similar to techniques employed in movie and television projectors or in laser beam shaping. An optical design for beam homogeneity control employing a mix of such techniques is shown in Fig. 9.1 .

These techniques are very effective, as one can see in beam profile power density measurements ( Figs. 9.2 and 9.3 ). “Top hat” profiles with planar power distribution with lower than 3% fluctuations can be found.


Optical Beam Aiming and Positioning, Auxiliary Aiming Beam
As crosslinking is highly dependent on the power density of an irradiated invisible light, special strategies to center the treatment on the patient’s cornea are required. A viable approach is to install a coincident visible aiming beam to guide the treatment. To minimize the patient’s discomfort, a deep red wavelength may be employed. The red beam is produced either by a red LED or by a low-power laser line or crosshair generator ( Figs. 9.4 and 9.5 ).


Owing to the necessary optical beam shaping and homogeneity control, the output beam reaching the cornea should have a subtle converging conical format ( Fig. 9.6 ) to allow a close-to-perpendicular incidence on the convex corneal surface. Gaussian-shaped beams are not recommended because they increase the heterogeneity of the energy delivered to the cornea.

Optical Beam Spot Size
Several UV sources on the market are equipped with a spot size selector, ranging from 5 mm to 25 mm. As power density should be maintained constant, an electronic control system must automatically correct the power emission to keep power density at the desired value ( Fig. 9.7 ).

The Main Electronic Control System
Crosslinking demands a very tight control of its parameters, especially regarding the nature of UV light and power density. In Fig. 9.8 , a common control diagram block of a crosslinking system is presented. It is based on the functional flow required to fulfill all clinical and safety regulatory standards.

Main Processor, Display, and Keyboard
Powerful microprocessors available on the market are used to control and continuously check power delivery, exposure time, energy density, and dose calculation with low cost and high reliability.
The display and keyboard section allow users to select desired parameters and command operations. Although touchscreen input devices are commonly used at present, they are inherently very sensitive to static discharges. Therefore medical-grade devices, which can sustain correct operation even when submitted to high static electrical discharges caused by cloth friction or gloves, must be employed.
After selection of desired clinical parameters, power density, spot size, energy dose, and exposure time, the software calculates all remaining parameters. Messages and values are presented on the display for a clearance to start the operation.
The emergency switch is a regulatory requirement, as in other medical devices. It allows one to immediately stop treatment in case of any device malfunction.
Watchdog Circuit
All microprocessor-controlled devices need software that may malfunction owing to external or internal disturbances or failures. Every medical-grade device must have some way to avoid damage in these cases. The conventional approach is to use a “watchdog” circuit. These circuits generate a periodic signal to check the microprocessor. If the microprocessor response does not match in time or in value, the watchdog circuit “resets” the microprocessor to a safe state. In addition, a direct link to the power control block halts all power delivered to the LED, emission is interrupted, and an error message issued to the operator.
In more sophisticated architectures, a secondary redundant processor can take control of the action and recover the mission, mainly in case of minor errors and small disturbances, without any user intervention.
The Power Control Block, Current Sensor, Main Photodiode Led Control Loop
The main control block is the circuit that ensures that LED UV emission remains within a very small error margin and will be kept constant independent of temperature variation and aging. After starting the procedure, the current/voltage applied to the LED device is continuously monitored and LED performance is compensated in real time. LED emission is sampled by optical means using a specific photodiode placed over the output optical system. The photodiode is a device that creates a current directly proportional to the direct light incident on it. A spectral filter above the photodiode ensures that only the wavelength corresponding to the LED UV emission is sampled to avoid any ambient or environmental interference on power delivery.
If the energy measured is above or below the safe operating range of the LED device, an error message is issued. This can occur owing to overheating.
Continuous and Pulsed Power Control
Oxygen availability is a limiting factor during riboflavin UV crosslinking treatment because it is one source of free radicals, which enable covalent collagen bridge formation. In the Dresden protocol, with its relatively low power density and long exposure time, this is not an issue because of the natural diffusion of oxygen into the cornea. However, with higher power density, the use of continuous energy delivery can deplete the oxygen available for crosslinking.
In higher-power density treatments, pulsed UV-light application was introduced as a new strategy to avoid this problem. Several studies report long biomechanical stability with this modified treatment.
Evaluation of patients submitted to continuous (30 mW/cm 2 for 4 minutes) or pulsed fast crosslinking (30 mW/cm 2 , 1 second on, 1 second off, for 8 minutes) demonstrated a mean depth of the demarcation line of 149.32 ± 36.03 µm and 213 ± 47.38 µm, respectively, which suggests a benefit of the pulsed delivery technique. Another study, using similar parameters of pulsed and continuous energy delivery, evaluated stromal alterations regarding keratocyte apoptosis by confocal microscopy after crosslinking with both strategies. It found that, with pulsed energy, there was a deeper apoptotic effect around 200 µm (range, 190–240 µm), while with continuous energy delivery, the apoptotic effect was detected around 160 µm (range, 150–200 µm). Although promising, this strategy needs to be studied further.
Auxiliary Devices
Interlock Device
One regulatory requirement is the interlock device. This interlock can be tied in a door switch to avoid nonauthorized entrance into the procedure room, a remnant of safety regulations originally intended for very-high-power invisible laser systems. This same device can be used to interrupt emission when attached to a patient head belt, ensuring that patient head movement is inside the beam alignment margin.
Sound Emission
Sound emission may indicate the presence of invisible light.
Aiming Beam, or Alignment Auxiliary System Control
As described earlier, there is an auxiliary device to allow correct beam placement over the cornea. There are several methods on the market, as described before. A visible LED source is used in most crosslinking devices. Its light intensity is selectable and closed loop controlled. During treatment, or during UV LED exposure, normally its light intensity is reduced to increase patient comfort.
Eye Tracker
As some crosslinking procedures take a long time to perform (30 minutes is a standard protocol), patients may move their heads, causing misalignment of the system. Some misalignment can decrease the effectiveness of the procedure and potentially cause damage to limbus stem cells. Therefore some manufacturers offer optional video eye trackers to check alignment in real time.
UV-Light Source
There are several UV-light sources, such as xenon discharge lamps, deuterium lamps, fluorescent mercury arc lamps, and high-temperature halogen lamps. Although these technologies can deliver considerable amounts of UV light, the light spectrum emitted is broad, and the spectral power density is very low in the UV region of interest for riboflavin-based crosslinking.
Initially, very-narrow-band interference light filters had been employed to allow only the UV region of interest to be delivered onto the corneal tissue. Therefore very-high-power sources and high-power electronics were needed at that time. The development of moderate-power LEDs in the UV spectral region changed this scenario in the beginning of the 21st century. Light emitting diodes had been established since the semiconductor revolution at the beginning of the 1960s. Initially, only infrared, red, and green emitting diodes were feasible, with progressively higher output power and broader visible spectral coverage. In the late1990s, consequent to new dopants and semiconductor structures, the development of LEDs composed of indium gallium nitride semiconductors allowed emission in the UVA spectrum (315–400 nm). An interesting history of the development and principles of operation of such blue and UV devices can be found elsewhere.
Briefly put, an LED emits photons in a predetermined spectral region owing its material constituents and the existence of enough density of charge carriers, electrons, by means of carefully controlled voltage and current applied. Medical use of LEDs is based on specific behavior and performance characteristics. Some of the most important subjects in this field will be discussed.
Wavelength Selection
Owing to its internal tolerances and material variations, a typical UV LED does not present a precisely tuned wavelength and viable devices must be selected in each production batch. For instance, a typical 365-nm device production batch shows around ±10 nm peak position distribution. Therefore when selecting the device, it is necessary to specify the tolerance of the desired wavelength. Factory standard selection classifies devices on ±3 nm peak position range bands. This tolerance centered on 365 nm is well inside the riboflavin/tissue crosslinking reaction confidence area.
Temperature Influence on Wavelength
As with any semiconductor, the peak wavelength varies with temperature. Typical variation values are about 0.02 nm/C° in LED UV devices, which is considered a very stable emission. Under the recommended operational range of temperature for clinical use and the assistance of a closed-loop power control, there is very low risk of wavelength slippage that could compromise its performance. Aging also influences semiconductor devices, and some wavelength deviation is possible, but all LED UV devices present on the market remain inside ± 2 nm through their entire lifetime.
Temperature Influence on Power Output
Power output is strongly dependent on semiconductor temperature. The performance of the LED decreases with increasing temperature. This dependency makes it impossible to control the device’s UV emission based only on a constant voltage or current. A closed-loop control must continuously sample the UV output power and modulate the current applied to reach the desired value at a certain time.
Wavelength Selection
Owing to its internal tolerances and material variations, a typical UV LED does not present a precisely tuned wavelength and viable devices must be selected in each production batch. For instance, a typical 365-nm device production batch shows around ±10 nm peak position distribution. Therefore when selecting the device, it is necessary to specify the tolerance of the desired wavelength. Factory standard selection classifies devices on ±3 nm peak position range bands. This tolerance centered on 365 nm is well inside the riboflavin/tissue crosslinking reaction confidence area.
Temperature Influence on Wavelength
As with any semiconductor, the peak wavelength varies with temperature. Typical variation values are about 0.02 nm/C° in LED UV devices, which is considered a very stable emission. Under the recommended operational range of temperature for clinical use and the assistance of a closed-loop power control, there is very low risk of wavelength slippage that could compromise its performance. Aging also influences semiconductor devices, and some wavelength deviation is possible, but all LED UV devices present on the market remain inside ± 2 nm through their entire lifetime.
Temperature Influence on Power Output
Power output is strongly dependent on semiconductor temperature. The performance of the LED decreases with increasing temperature. This dependency makes it impossible to control the device’s UV emission based only on a constant voltage or current. A closed-loop control must continuously sample the UV output power and modulate the current applied to reach the desired value at a certain time.
The UV Light Optical Beam Delivery System
Key factors of crosslinking equipment are optical beam output shaping and control.
Optical Output Power Density Distribution
Many of the UV LED sources employed in crosslinking procedures are selected owing to their power output requirements. Unfortunately, in the required power range, all devices are composed of a group or an array of very small emitters tied together, assembled and electrically connected on the same thermal substrate. Consequently, the light-emitting surface is not homogeneous and shows very strong power variation and power density fluctuation. This characteristic imposes a critical constraint as the riboflavin/tissue interaction is highly dependent on power density. Therefore the optical system must employ techniques to create a virtual source with a homogeneous profile. Otherwise, a heterogeneous power distribution on the corneal surface may cause differential deformation, called hot spots . Hot spots may cause nonuniform results and localized endothelium cell damage and haze, especially in thin corneas.
Fortunately, there are several optical design methods that can be employed that are similar to techniques employed in movie and television projectors or in laser beam shaping. An optical design for beam homogeneity control employing a mix of such techniques is shown in Fig. 9.1 .
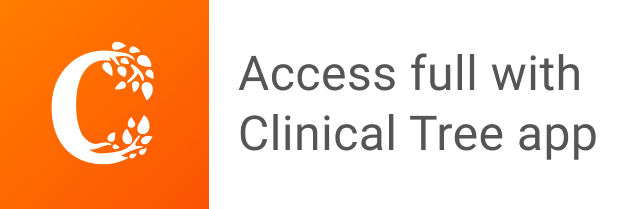